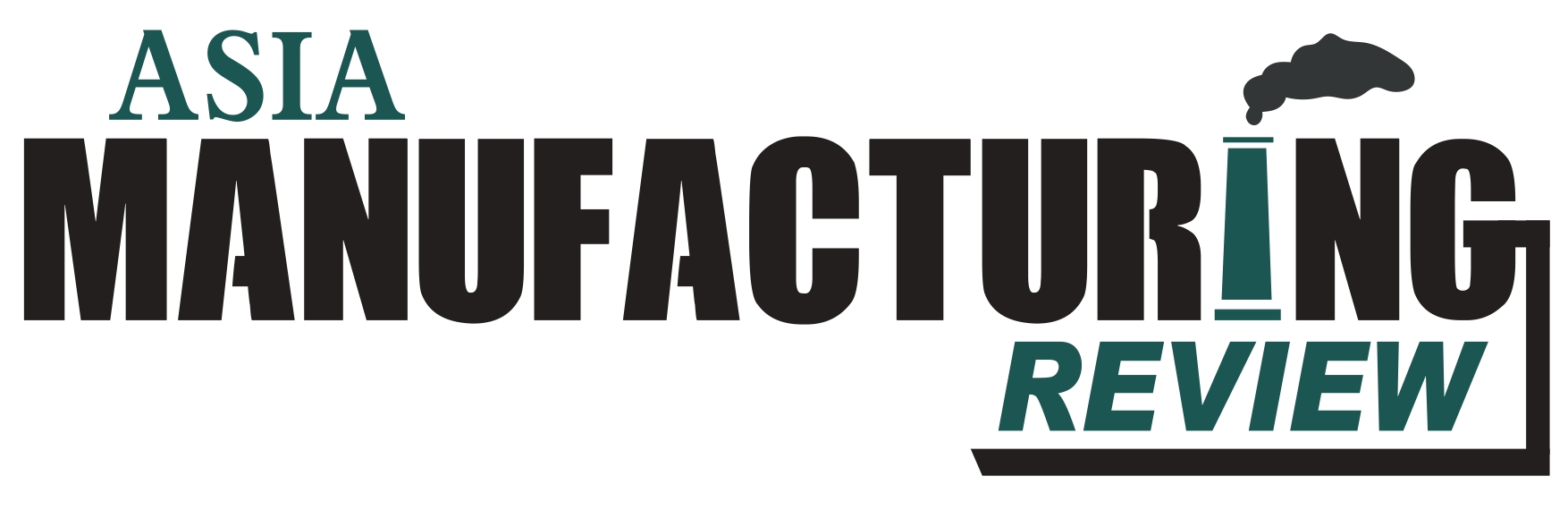
The awareness of the need for high-quality anti-vibration mounts is on the rise as manufacturers and sectors such as railways understand the importance of noise reduction and vibration control. Driven by this increasing awareness, the Malaysian anti-vibration mounts market is poised for substantial growth. According to research, the sector is evaluated at $6.3 billion in 2022 and is projected to reach $7.8 billion by 2030. However, the demand for high-quality products at a competitive price is the need of the hour. By maintaining rigorous quality standards, GMT (Gummi Metall Technik) Malaysia, a subsidiary of GMT Germany, made it a trusted name across various sectors, including railway, construction, marine, and defense industries.
GMT Malaysia has been a provider of high-quality anti-vibration solutions since its inception in 1980. Despite the market being flooded with low-quality products, the company has distinguished itself through its unwavering focus on quality, supported by technical expertise from its German counterpart. While good quality often comes at a higher price, its strategy is to ensure that the products meet all specifications and requirements across sectors. The company’s approach is holistic, providing products, solutions, and services. Unaware of the specifics needed for their applications, many clients rely on it for comprehensive support and guidance.
The Malaysian firm’s manufacturing processes mirror those of its parent organization in Germany, ensuring consistent quality from raw materials to finished products. The company conducts its compounding, vulcanization, and bonding processes in-house, maintaining strict quality control at every stage. “We have a robust engineering team backed by the technical expertise of GMT Germany,” said K Sivanjothi, Director at GMT Malaysia. “For all our design and technical requirements, we still consult closely with GMT Germany.” This ensures that every process the Malaysian arm follows aligns perfectly with the high standards set by the German counterpart. “By mirroring its procedures, we maintain the same level of excellence and precision in all our operations,” adds Sivanjothi.
Suspension Systems & Military Tank Parts
The railway sector is a significant focus for GMT Malaysia, with the company supplying a wide range of products for primary and secondary suspension systems. These include conical springs, Chevron springs, and spherical bearings, all produced locally in Malaysia to exacting standards. These parts have been supplied to SRT, ARL Thailand, LRMC Philippines, SMRT Singapore and local entities like Express Rail Link, SMH Rail, Prasarana, KTMB, Rapid Rail, with development ongoing for the Indonesian and Taiwan market. Samples are mounted on trains for several months of operation before final approval. The Malaysian firm has supplied these high-quality parts to Thailand for over a decade, establishing a solid track record without any quality issues. The products are also used in Southeast Asian railways, including Indonesia and the Philippines.
GMT provides air spring systems for secondary suspension, manufactured exclusively in Germany due to the specialized production required. These air spring systems are developed with years of expertise and are supplied to local users, maintaining the same high-quality standards. Each product undergoes thorough trials, specification compliance checks, and necessary tests on materials and finished products before being provided to customers.
Apart from the primary and secondary suspension systems, GMT, in collaboration with Pandrol, manufactures bonded DFF base plates for the tracks. Similarly, the base plates sample undergoes rigorous testing at Pandrol, France and independent testing laboratories to meet the required specifications before mass production. GMT base plates are being used in Malaysia, Taiwan, and Canada.
For military applications, the firm operates its in-house testing facilities, ensuring that the materials used are rigorously tested and approved to meet German standards. It utilizes the same production recipes in Malaysia, integrating internal lab and field tests into its processes. Serving the replacement market, the company designs materials and products based on customer specifications, providing samples for customer testing before proceeding to mass production. The meticulous approach has been in place since 2009, initially supplying parts for Leopard tanks and the M113 in Malaysia and now extending to parts for the PT-91. Each product undergoes comprehensive internal testing for rubber compounds to meet all specifications, followed by trials and customer testing. Only after successful customer testing do orders proceed to mass production.
The Think Tank
An ISO-certified company, GMT Malaysia has a dedicated internal laboratory led by Dr Puspa, a specialist in polymer science. The laboratory is equipped to conduct extensive rubber material testing, including basic tests for tensile strength, elongation, and compression set. In addition, it possesses advanced machinery for stiffness testing and dynamic testing of finished products. Plans include upgrading the dynamic testing machine to the latest technology and ensuring continuous improvement in quality assurance. For railway components requiring 100 percent product testing due to their critical safety nature, the company employs state-of-the-art equipment to thoroughly test the material and the finished products. The approach, coupled with robust technical support from Germany, provides it with a significant advantage in ensuring the reliability and safety of its offerings.
GMT Malaysia has evolved significantly since its inception as Rubber Metal Technik in 1980. The company began with bridge-bearing projects, supplying the Penang Bridge, before expanding into the automotive sector. As the automotive industry became increasingly competitive, the company shifted its focus to high-end products for the railway and construction machinery sectors. The strategic shift allowed the company to leverage its expertise in high-value-added products, ensuring sustainable growth. A consistent focus on quality and customer satisfaction has marked its growth trajectory. It now covers Southeast Asia, including Taiwan, China, and Pakistan.
GMT Malaysia’s journey from a small operation to one of the key players in the anti-vibration mounts market is a testament to its commitment to quality, innovation, and customer-centricity. The company’s ability to adapt to market changes, coupled with its robust R&D and testing capabilities, positions it well for future growth. As the demand for high-quality anti-vibration solutions continues to rise, it is well-equipped to meet the needs of its customers, both domestically and internationally. The commitment to excellence and continuous improvement ensures that the company will remain one of the trusted partners in the industry for years to come.
We use cookies to ensure you get the best experience on our website. Read more...