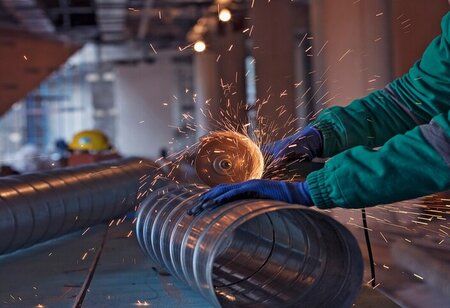
The boundaries between the physical, digital, and biological worlds are becoming increasingly hazy in the Fourth Industrial Revolution due to a synthesis of technologies such as artificial intelligence, robots, the Internet of things, blockchain, quantum technologies, and many more.
The agents of change are not consistent, even while the change itself is. The agents modify and adjust the game's dynamics more drastically than in the previous iteration, building on the lessons discovered. There are many examples in the field of industry. These levers of change have sparked revolutions that affect all facets of life and society, not simply those related to business, rather than just cosmetic changes or bettering the way industry operated in the past.
The first Industrial Revolution was driven by steam, which was expanded upon by electricity to power the second. The Third Industrial Revolution (IR) was driven by early automation, and the Fourth IR is currently being propelled by intelligent computers in a way that hasn't been considered by society previously.
The boundaries between the physical, digital, and biological worlds are becoming increasingly hazy in the Fourth Industrial Revolution due to a synthesis of technologies such as artificial intelligence, robots, the Internet of things, blockchain, quantum technologies, and many more. It is quickly becoming into an essential component of life and beyond. To survive, one must be able to adjust to these changes.
With experience centers and a vibrant environment for its adoption, initiatives like SAMARTH Udyog Bharat 4.0, spearheaded by the Indian Ministry of Heavy Industry, have been instrumental in propelling Industry 4.0 forward in India. The steel industry, like all others, is embracing Industry 4.0 at a rapid pace. The goal of this ambitious initiative is to reach the 300 million tonne capacity by 2030, while simultaneously increasing efficiency and safety and promoting environmental goals. The second-largest steel industry globally is found in India. It accounts for 1/8 of the GDP of the country's manufacturing sector.
Security of raw materials is essential to India's plan to increase its steel production. It is anticipated that the demand for iron ore, coking coal, ferro alloys, and other materials would rise in terms of both quantity and quality. AI techniques must be used to search for, locate, and develop new mines using the enormous amount of data that the Indian Steel Plant and the Geological Survey of India have to provide.
Producing virtual twins of real plants, known as digital twins, may help make well-informed decisions, especially when it comes to areas like blast furnaces, and provide useful insights and simulations to enhance plant performance. The Indian steel industry will not be a follower but a leader in implementing cutting-edge technology to build cutting-edge, productive steel mills as sustainability takes center stage on a global scale. It's also worthwhile to investigate the idea of using digital twins with disaster management systems.
The steel industry will secure the country's advancement and competitiveness in the global market through strategic investments, cooperative efforts, a firm focus on digitalization, and the availability of a thriving Indian start-up ecosystem for developing focused software as a service model and tapping into ongoing revolutions in IoT, 5G, drones, and digitalization.