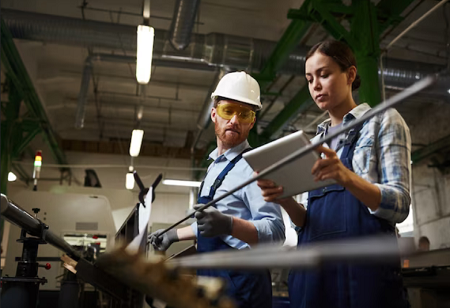
On Friday, Taiwan and India entered into a pact to bring Indian migrant workers to the island. This move comes as Taipei, facing a shortage of labor, aims to diversify its foreign workforce from the usual countries of Southeast Asia. The Ministry of Labour in Taiwan announced that a mutual agreement was reached between their unofficial embassies in Taipei and Delhi. However, they still need to finalize the specific arrangements for execution. According to the ministry, the need for workers in Taiwan across various industries such as manufacturing, construction, agriculture, and others has consistently grown. However, Taiwan is unable to meet this demand on its own. Consequently, there has been a yearly increase in the demand for migrant workers.
"The quality of Indian labour is stable, they are hardworking and well considered," the ministry said.
The statement mentioned that initially, a pilot scheme on a small scale will be initiated. If the pilot scheme is successful, it implied that more Indian workers would be permitted to come, although no specific number was mentioned, and it was clarified that Taiwan will be responsible for determining the final numbers. Taiwan has previously refuted claims that it could permit the entry of around 100,000 Indian workers.
The manufacturing landscape in Asia has undergone significant transformations over the years, evolving into a powerhouse for global production. While the region offers competitive labor costs, the challenge lies in maintaining high-quality standards amid cost pressures. Manufacturers who can successfully manage cost pressures while prioritizing quality are expected to endure the ongoing crisis and ultimately emerge stronger and more resilient. This article informs us about the strategies and considerations for achieving a delicate equilibrium between labor costs and product quality in Asia's manufacturing sector.
Digital transformation
Digital transformation is crucial, particularly in the manufacturing industry, especially in Asia, in order to attain optimal operational efficacy. Manufacturers need to embrace intelligent factory technologies like the Internet of Things (IoT), automation, robotics, and advanced data analytics.
These technologies have the potential to make production processes more efficient, minimize human mistakes, and offer immediate knowledge about operations. As a result, decision-making can be enhanced, and businesses can swiftly respond to market fluctuations. In Asia, automation may face cultural opposition due to the traditionally low labor costs. However, the long-term advantages of enhanced quality and efficiency can greatly outweigh the primary investment and adaptation hurdles.
For instance, about three years ago, the Indian division of the American food giant Kellogg's, which has been doing business in India for nearly thirty years, began a digital transformation program.
According to Prashant Peres, MD for South Asia at Kellogg, “In the first leg of its project, the company digitised its communication processes that helped it keep the business running during the first Covid-19 wave. Motivated by that, it has deployed the programme to transform its supply chain, product development and go-to-market strategy as well. “Based on the principle of ‘customised off-the-shelf’ strategy, we decided to customise our products based on specific consumer needs instead of trying to invent products on our own every time,” he says
Subsequently, they have partnered with Ivy Mobility, a consumer goods technology provider, to digitally transform their distribution management system.
Supply Chain Disruptions
Asian manufacturers need to establish robust supply chains in order to minimize the impact of disruptions, including those triggered by the COVID-19 pandemic or geopolitical conflicts. This entails expanding the sources from where we obtain materials, enhancing transparency using digital tracking systems, and creating backup strategies in case there are disruptions in the supply chain.
Developing stronger connections with nearby suppliers has the potential to reduce the length of the supply chain and improve its level of reactivity. Implementing technologies such as blockchain can further boost the ability to track and secure every step of the supply chain, thus ensuring the authenticity of materials and components.
Gesa Schneider, the senior territory manager of Central Europe for the 3D printing software company Markforged says that “Once 3D printing is more widely adopted, she believes the manufacturing process will be able to transform supply chains for the better.”
Lean manufacturing
The principles of Lean Manufacturing play a vital role in eliminating waste and enhancing productivity. Asian producers have the ability to utilize lean methods to streamline the production process, diminish the amount of stored inventory, and enhance the overall quality.
Methods like 5S, Value Stream Mapping, and just-in-time (JIT) inventory have the potential to reveal and eliminate inefficiencies, resulting in a more efficient operation. Developing a Lean Culture that involves every employee in Continuous Improvement has the potential to enhance resilience and flexibility when confronted with shifting market requirements.
Toyota Motor Corporation, Japan is renowned for its implementation of lean management principles in manufacturing, which entails a strong emphasis on continual enhancement, waste minimization, and valuing individuals.
Panasonic Automotive Systems implemented a program known as Gemba Innovation with the objective of enhancing their onsite operational abilities. By utilizing the strengths of each company within Panasonic Group, such as incorporating advanced AI technologies from Panasonic Connect Corporation, the initiative successfully boosted productivity while also decreasing the time and effort required for analysis.
Kaizen
The philosophy of Kaizen, which focuses on constant improvement, has the potential to be incorporated into all aspects of a business. Manufacturers can foster a climate of continuous innovation and adaptation by enabling employees at every level to recognize and address areas that need improvement. This holds special importance in the ever-changing manufacturing industry of Asia, where even small advancements can result in significant benefits in terms of quality, cost, and timely delivery, thus giving a competitive edge.
Sony has successfully utilized Kaizen principles to enhance its production procedures and sustain its competitiveness in the global market for an extended period. This achievement can be attributed to the strong conviction of Akio Morita, the company's founder, who recognized the significance of constant improvement.
Honda has adopted Kaizen in its manufacturing facilities to attain elevated levels of productivity and diminish expenses.
Quality Management and assurance
It is crucial for manufacturers, especially in Asia where quality perception can differ, to incorporate strong Quality Management and assurance procedures in order to meet customer expectations and adhere to international standards.
Implementing well-established quality systems like ISO 9001 can assist in streamlining procedures, lowering the rate of errors, and diminishing the need for repeated tasks. Consequently, this enhances customer contentment and decreases expenses.
Canon's utilization of Kaizen has played a crucial role in its Canon Production System (CPS). CPS has aimed to produce higher quality goods with reduced expenses and ensure faster delivery. The CPS system consists of three fundamental structures: quality assurance (QA), production assurance (PA), and personnel training (PS) systems. An effort has been made by these structures to achieve manufacturing on an as-needed basis, rapid delivery, affordability, and the ability to visually monitor operations.
Industry 4.0
Asia-based manufacturers should contemplate embracing Industry 4.0 technologies to amplify connectivity, automation, Machine Learning, and real-time Data Analysis in order to improve production efficiency. Through the incorporation of cyber-physical systems in the manufacturing process, organizations have the ability to establish a manufacturing environment that is more flexible and responsive, enabling it to effectively endure disturbances and market fluctuations.
“Today's manufacturing industry aims to leverage the power of advanced technologies such as artificial intelligence (AI) and Big Data to achieve increased efficiency and productivity in supply chain and operations,” says Ankush Khanna, Director- Commercial Brand Marketing (South Asia Pacific), ExxonMobil.
“Furthermore, an enterprise connected by IIoT enjoys several benefits in ensuring business continuity despite restrictions, allowing more flexible workflow management that is suited to the ‘new normal’ and encouraging innovation for better productivity and output. Simultaneously, it enhances security, reduces downtime, and significantly cuts maintenance costs,” he adds.
Data analytics
The use of data analytics has the potential to revolutionize manufacturing operations through the provision of valuable information on production patterns, detection of inefficiencies, and anticipation of maintenance requirements. Asian manufacturers can achieve cost savings and improve service levels by investing in data analytics platforms. These platforms enable them to enhance Quality Control, accurately predict demand, and optimize supply chain operations.
Toshiba Corporation utilized data analytics to implement predictive maintenance, a Lean principle that focuses on minimizing downtime and cost reduction by proactively identifying potential equipment failures beforehand. Given that the average manufacturing plant incurs costs of over US$172 million per year due to downtime, any decrease in such costs can be regarded as beneficial.
Effectively managing both labor expenses and product quality in Asia's manufacturing sector presents a complex hurdle that necessitates a thoughtful, comprehensive, and flexible methodology. Manufacturers can strike a favorable equilibrium between cost competitiveness and maintaining high-quality standards by giving thoughtful attention to various aspects like labor expenses, automation, enhancing skills, optimizing the supply chain, and complying with regulations. The future of Asia's manufacturing success will be built on the pillars of embracing innovation, promoting collaboration, and instilling a culture of constant improvement.