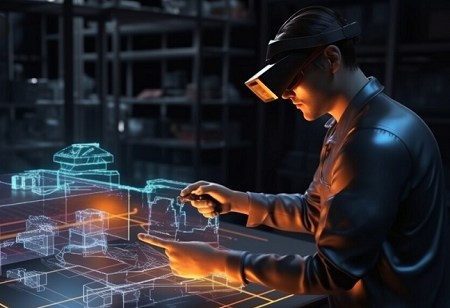
Cisco has been recognized as winner of the “IoT Security Innovation of the Year” and “Smart Manufacturing Solution of the Year” awards in the 8th annual IoT Breakthrough Awards program. This recognizes the company’s breakthrough innovation of an integrated architecture that converges networking and security, allowing industrial networking equipment to both connect and protect, thereby avoiding the need for additional hardware. In today's Industry 4.0 era, using the Internet of Things (IoT) in manufacturing is changing the game. This technology is turning old-fashioned manufacturing into a smarter, more automated, and efficient system, known as "smart manufacturing." With IoT, manufacturers can boost productivity, cut costs, and make their operations run more smoothly.
"IIoT offers real-time insights, predictive maintenance, and unparalleled efficiency. This technology not only enhances productivity but also reduces human intervention in repetitive tasks, allowing workers to focus on higher-value activities such as creativity and decision-making”, mentioned Pravin Panchagnula, Executive Director and Head of Manufacturing at Microsoft India to the media.
The primary objective for incorporating IoT in manufacturing is driven by the necessity for real-time data insights, predictive maintenance, and enhanced operational efficiency.
Informed Decision Making with Real-time Data
One of the main reasons for using IoT in manufacturing is the ability to collect and analyze real-time data. Traditional systems often depend on periodic data collection and manual reporting, which can cause delays and errors. In contrast, IoT devices continuously gather data from different spots on the production floor, offering a steady flow of information.
To give an example, General Electric (GE) has implemented IoT solutions in its manufacturing plants to monitor the performance of its machines. Sensors installed on equipment capture data on temperature, pressure, vibration, and other critical parameters. This data is then analyzed in real-time to identify deviations from optimal operating conditions.
“IoT is a game-changer for the manufacturing sector, allowing for real-time operational insights and process optimization. This technological advancement is crucial for staying competitive in a rapidly evolving industrial landscape”, mentioned Marc Jarrault, MD of LAPP India to the media.
Reducing Downtime through Predictive Maintenance
Unexpected equipment failures can cause major downtime and expensive repairs, messing up production schedules and impacting profits. Predictive maintenance, powered by IoT technology, helps solve this problem by predicting equipment failures before they happen. IoT sensors keep an eye on machine conditions and forecast potential issues based on data patterns.
In this regard, Harley-Davidson provides a compelling example of how predictive maintenance can transform manufacturing operations. The iconic motorcycle manufacturer integrated IoT sensors throughout its production line to monitor machine health. By analyzing the data collected, Harley-Davidson can predict when a machine component is likely to fail and perform maintenance proactively.
"IoT is the single biggest technological innovation that will enable manufacturers to achieve greater levels of efficiency and agility. The Industrial Internet is about connecting big data, big machines, and people to drive unprecedented efficiency and productivity”, mentioned Jim Heppelmann, President & CEO, PTC.
Boosting Flexibility and Operational Efficiency
Integrating IoT boosts operational efficiency by automating tasks and cutting down on manual work. Smart devices and connected systems allow machines to communicate effortlessly, streamlining workflows and reducing human errors. This automation not only accelerates production but also helps manufacturers quickly adapt to market changes.
To give an example, Siemens has successfully implemented IoT in its electronics manufacturing plants. By using IoT-enabled robots and automated quality control systems, Siemens can quickly adapt its production lines to manufacture different products without extensive reconfiguration. This flexibility allows Siemens to meet varying customer demands efficiently, providing a competitive edge in the market.
“The International Telecommunications Union (ITU) defines IoT as 'a global infrastructure for the information society, enabling advanced services by interconnecting (physical and virtual) things based on existing and evolving interoperable information and communication technologies", mentioned Aiyappan, Founder, Congruent Services and Senior Member of IEEE.
The future of IoT in manufacturing looks bright, with ongoing tech advancements driving more innovation. The arrival of 5G technology will boost IoT integration by offering faster and more reliable connections. This will allow manufacturers to use more advanced IoT solutions, like real-time remote monitoring and control of production processes.
Additionally, improvements in artificial intelligence (AI) and machine learning will enhance IoT devices' capabilities. AI algorithms can process large amounts of data from IoT sensors, providing deeper insights and more accurate predictions. This blend of IoT and AI will lead to the next wave of smart manufacturing, featuring unprecedented levels of automation and intelligence.