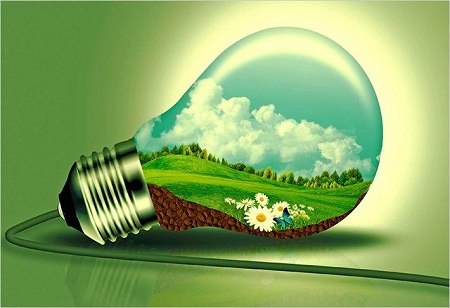
When thinking about companies that prioritize the environment, Apple and other tech giants are not the first ones that come to mind immediately. Despite being located in Cupertino, CA, this well-known company remains dedicated to sustainability. Their specific concentration is on three fundamental areas: reducing the influence on the climate, safeguarding natural resources, and introducing safer materials into both products and work environments. Based on this belief system, Apple has implemented several wind and solar farms. These energetic sources play an active role in fueling their data centers, retail stores, and corporate offices. By using renewable energy sources, the tech sector set an admirable example for environmental responsibility.
Furthermore, Apple places importance on conserving materials. By improving the efficiency of production, utilizing renewable resources, and creating durable products, they greatly decrease the amount of waste generated. Apple's dedication to a sustainable future is emphasized by the fact that this strategy not only saves resources but also safeguards them.
In an era where environmental consciousness is becoming increasingly integral to business strategies, green manufacturing stands out not only as a commitment to sustainability but also as a pathway to improved profit margins. Energy efficiency at the heart of this transformative approach, offering manufacturers an opportunity to reduce costs, enhances operational efficiency, and contributes to a greener future. This article explores in detail how businesses can strategically leverage energy-efficient practices in green manufacturing to achieve sustainable prosperity.
The urgency of addressing environmental concerns has never been more apparent. Climate change, resource depletion, and environmental degradation underscore the need for industries to adopt sustainable practices. Green manufacturing emerges as a solution that aligns profitability with ecological responsibility. Beyond altruism, there is a compelling business case for adopting green manufacturing practices. Consumers increasingly favor environmentally conscious products, and regulatory frameworks are evolving to incentivize sustainable operations. Green manufacturing is, therefore, not just a moral imperative but a strategic advantage.
Energy Audits and Benchmarking
The journey towards energy efficiency begins with a thorough energy audit. By scrutinizing current consumption patterns, manufacturers can identify areas of wastage and inefficiency. Benchmarking against industry standards provides a basis for setting realistic improvement targets.
Upgrading machinery and equipment to energy-efficient models is a crucial step. This not only reduces energy consumption but also often leads to enhanced operational performance and longevity of assets.
Energy efficiency is greatly influenced by the layout and structure of manufacturing facilities. Creating a sustainable working environment is achieved by implementing elements like natural lighting, insulation, and energy-efficient HVAC systems, in addition to reducing operational expenses.
Leveraging technology and innovation to ensure a lean and green manufacturing setup that can drive renewable and sustainable practices is key to driving long-term business benefits, says Srinath Ramakkrushnan, Co-Founder & COO, Zetwerk Manufacturing.
Renewable Energy Integration & Operational Optimization
The integration of renewable energy sources like solar, wind, or geothermal power presents a significant opportunity. Assessing the feasibility of these sources based on location, cost, and available technology is the first step towards making a meaningful impact. Incentives, subsidies, and tax credits can significantly offset the initial costs of adopting renewable energy sources, making it a financially viable choice.
Optimizing production schedules to minimize energy consumption during non-peak hours is a simple yet effective strategy. This requires a comprehensive understanding of energy usage patterns and a commitment to aligning production with periods of lower energy demand.
Implementing real-time energy monitoring systems enables manufacturers to identify and address operational inefficiencies promptly. This data-driven approach empowers businesses to make informed decisions that optimize energy consumption.
Honda is deeply dedicated to sustainability in a remarkable way. The objective of its "Green Path" is to minimize and eventually eliminate the utilization of harmful substances and limited natural resources. It also aims to create products that can be easily recycled, while reducing water wastage and CO2 emissions throughout the manufacturing process.
Supply Chain Sustainability
Sustainable practices should extend beyond the manufacturing facility. Collaborating with suppliers who adhere to eco-friendly standards ensures a holistic approach to green manufacturing.
The logistics and transportation aspects of the supply chain are often energy-intensive. Streamlining transportation routes, adopting fuel-efficient vehicles, and leveraging technology for efficient inventory management can contribute to significant energy savings.
“If you want to help save the environment, we all need to learn to manage production processes in an eco-friendly way, manufacture eco-friendly products and maintain the whole supply chain to minimize pollution, carbon emission, waste and release of Toxic materials. Along with this, we should all take the responsibility as a manufacturer and as an individual to recycle most of what we produce including the waste,” says Dr. Unmesh Jagtap, CEO, Sonnenschein Engineering & Infra LLP.
Waste Reduction and Recycling
Implementing waste reduction programs not only minimizes environmental impact but also contributes to cost reduction. By optimizing processes and promoting a culture of resource efficiency, manufacturers can reduce material wastage.
Establishing recycling initiatives for materials used in the manufacturing process completes the sustainability loop. Repurposing waste materials not only minimizes landfill contributions but also conserves energy compared to the production of materials.
When it comes to recycling and reusing, HP and Dell are at the forefront of computer manufacturing. The company is reducing its environmental impact by enabling customers to bring in their old computers, printers, and even ink and toner cartridges for recycling. Indeed, HP has repurposed over 875 million ink and toner cartridges. To produce new HP ink and toner cartridges, HP has utilized over 4.7 billion recycled plastic bottles and 114 million plastic clothes hangers. There will be more enhancements in the future as well.
Dell has made a pledge to use entirely recycled or renewable material for its packaging, and at least half of its products by the year 2030.
Energy Management Systems (EMS)
Implementing Energy Management Systems (EMS) allows manufacturers to monitor, analyze, and control energy consumption in real-time. This proactive approach enables quick identification of areas for improvement and responsive adjustments to optimize energy usage.
Utilizing data analytics in conjunction with EMS provides insights into energy consumption patterns. Manufacturers can leverage this information to identify trends, set informed goals, and continuously improve energy efficiency strategies.
“Significant market opportunities are being created in India in various sectors, ranging from digital and electric solutions to renewable technologies, all a result of the new focus on sustainability,” says Venkat Garimella, Vice President, Strategy & Sustainability, Schneider Electric India.
“We are seeing an evolving landscape of Distributed Energy Resources (DERs), Energy Storage, Peer-to-Peer (P2P) energy trading, Green Hydrogen, supported by next-generation technologies like Smart Grid, Artificial Intelligence, Machine Learning, and Blockchain,” he adds.
The continuous improvement culture plays a vital role in ensuring the long-term success of green manufacturing initiatives. Motivate employees at every organizational level to share their thoughts, explore innovative technologies, and proactively find ways to improve energy conservation. The realm of green manufacturing is constantly evolving, as new technologies and improved methods consistently transform the overall scenario. It is essential for manufacturers to keep themselves up-to-date with the most recent advancements and be open to adjusting their approaches in order to integrate new and improved technologies that offer greater efficiency.