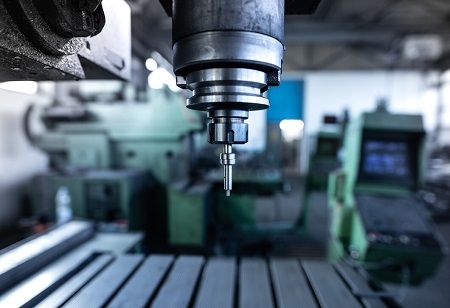
In December, 2023, Siemens introduced the Virtual Product Expert (VPE). VPE is a new support program for Siemen’s machine builders, machine tool users, dealers & importers. By using the VPE program clients can directly interact with a SINUMERIK CNC product expert. And, through this they can have a specific operation & programming questions answered.
John Meyer, the marketing communications manager for the Siemens Machine Tool Business, notes, “With the rapid advancement in our SINUMERIK CNC technology on both the automation hardware and software sides, we see our Virtual Product Expert program as a vital part of our support offering.”
Computer Numerical Control Machines or popularly known as CNCs have become a standard in the machining industry as the speed, ease of use & accuracy makes them indispensable tools. The types of CNC machine include CNC laser machines, CNC router machine, CNC milling machine, CNC laser cutting machine and others. However, CNC machines are still not perfect and quality control remains as one of the essential steps to identify and avoid defects, since many facilities have sub-par CNC quality control systems.
Although errors are far less likely with Computer Numerical Machines when compared to manual processes, errors can still occur. And when they occur, they lead to bottlenecks and in turn resulting in waste. Furthermore, if these are not identified in the beginning they can hamper client-customer relationships via poor-quality products. On the other hand, an effective quality control program enhances the whole machining process by terminating these errors. In this article let us look at the various ways at which how quality control in manufacturing can be enhanced with CNC machining.
Check the raw materials before machining & use the appropriate type of machine
Often people think that a quality check is a final step in the manufacturing process. Although final checks are highly important, quality control should begin early on. Early checks can avoid waste and detecting errors after machining is too late to recover costs. A crucial step in ensuring quality right from the beginning is checking the quality of the materials used for production. CNC machines can eliminate human error virtually, however if they are working either with defective materials or low quality it will not matter. Even a highly accurate system will give render products with poor quality if the materials used are not up to the mark.
Employees should check the quality of raw materials prior to using them in the manufacturing process in order to prevent these mistakes. Sourcing raw materials from trusted suppliers will help in decreasing several material-related issues, however, machinists cannot afford to take any kind of risks here. Workers can ensure they utilize their CNC machines to their full potential by either looking for various cracks, any defect in their material or even weak points.
Not all CNC machines are manufactured equal and hence companies should keep this in mind while addressing CNC quality control. Using an inappropriate machine for any specific task can lead to numerous errors. Hence, facilities should be selective regarding what orders go through what machines. Also, the more complex a product is, the more advanced its CNC machine should be.
The most common type for mechanical parts – a 3 axis CNC machine, is adequate for simpler designs but cannot be implemented beyond it. For products or parts that are even more complicated, workers should be using a four or five-axis machine. More axis render machines more precision, which enables them in performing more complex tasks without any error.
However, this does not mean that facilities should be implementing only 4 or 5 axis machines, balancing work among various machines can facilitate in reducing bottlenecks & make the overall operation efficient. More and more complicated designs must be sent to higher-axis machines as factories go about this balancing. Some of the top CNC companies in include Mori Seiki, Hyundai Wia, Toyoda, and Yasda.
Employ on-machine inspection
During the CNC machining process, machining processes can include quality control steps and devices known as machine tool probing systems attach to CNC machines & inspect quality as they start working. This on machine inspections help facilities to address & correct issues as they come up and eliminate/avoid errors in the final products.
Since examining routines that do not interrupt or interfere with the machining process, we can add them easily as it will not hinder efficiency. However, they will automatically redirect machines to the correct issues that are being detected in real-time. By catching errors and correcting them early, substantial mistakes can be prevented and which will in turn help in reducing the defective or poor-quality components down the line.
On machine inspection decreases quality control bottlenecks along with reducing scrap. Ensuring efficiency in this operation is highly important as machining time is the primary cost driver for the segment.
“Customers of machine tools industry often face several pain points such as complexity of operating intricate components; Downtime due to machine breakdowns or maintenance, expenses can strain budgets, and primarily shortage of skilled CNC operators and programmers,” says Indraneel Bhattacharya, Vice President, Sales & Marketing, Lakshmi Machine Works.
Use multiple quality control methods
How CNC machining itself is not perfect, all quality check methods possess unique merits and demerits. A single process alone cannot identify every error which may arise. Facilities should leverage numerous CNC quality control methods in order to make sure mistakes missed by a single process will not pass further to the next process.
Some of the top CNC machine manufacturers in Japan include AMADA, Okuma, Yamazaki Mazak and others.
The order of quality control method is highly imperative which includes numerous options as well. To be specific, human inspections may often be the last step, which should be the case with all-automation-reliant processes. Also automated checks most often are highly effective however; technical issues can increase and stop the accuracy. Furthermore, adding manual checks which can last can identify these potential errors.