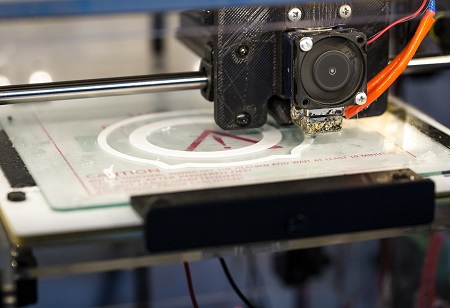
Advanced materials are at the forefront of revolutionizing 3D printing, unlocking new horizons of creativity and functionality. These cutting-edge materials, ranging from high-performance polymers to metal alloys and biocompatible substances, are reshaping industries. In aerospace, they enable the production of lightweight, intricate components with superior strength. Medical applications harness biocompatible materials for customized implants and prosthetics. In consumer goods, vibrant colors and textures expand design possibilities. Moreover, sustainability gains momentum as recycled and eco-friendly materials reduce waste. With these innovations, 3D printing is not just manufacturing; it is a realm of limitless possibilities, limited only by the imagination and material science's ever-expanding boundaries.
Let us look at three most important materials that are particularly notable in this regard and are giving an overhaul to 3d printing.
Carbon Fiber-Reinforced Composites
Carbon fiber-reinforced materials are transforming 3D printing by enhancing strength and stiffness while maintaining low weight. These composites are used in aerospace, automotive, and sporting goods industries to create lightweight, high-performance parts. They offer excellent structural integrity and can withstand extreme conditions, making them valuable for applications requiring durability.
In aerospace, carbon fiber-reinforced materials are becoming indispensable for aircraft components, where weight reduction is critical for fuel efficiency and performance. These advanced composites enable the creation of aircraft components that are not only exceptionally lightweight but also exhibit superior structural strength, enhancing safety and fuel economy. In the automotive sector, carbon fiber-reinforced 3D-printed parts are revolutionizing vehicle design, from lightweight body panels to intricate interior components, contributing to reduced emissions and improved overall efficiency. Moreover, in the sporting goods industry, these materials are reshaping the way high-performance equipment is manufactured, resulting in lighter and more responsive products that give athletes a competitive edge.
Metal Powders for Metal 3D Printing
Various metal powders, including titanium, aluminum, stainless steel, and nickel alloys, are being used in metal 3D printing processes like selective laser melting (SLM) and electron beam melting (EBM). Metal 3D printing allows to produce complex, high-precision metal parts, making it essential in aerospace, medical, and automotive industries. These materials enable the creation of components with exceptional mechanical properties and heat resistance.
The versatility of metal powders in 3D printing has opened up a world of possibilities for manufacturing industries. In aerospace, metal 3D printing is integral to producing intricate yet robust components, such as turbine blades and lightweight structural elements, which not only improve fuel efficiency but also enhance aircraft performance and safety. The medical field benefits from this technology with the ability to create custom implants and prosthetics tailored to individual patient needs, ensuring a precise fit and improved patient outcome. Furthermore, the automotive sector relies on metal 3D printing to fabricate engine components and lightweight parts that enhance vehicle efficiency and overall durability, contributing to the advancement of modern automotive engineering.
Biocompatible and Bioink Materials
Biocompatible materials are revolutionizing 3D printing in the field of medicine and biotechnology. Bioinks are used for bioprinting, enabling the creation of tissues and organs for research, drug testing, and even transplantation. These materials are designed to mimic the properties of human tissues, making them crucial in regenerative medicine and personalized healthcare.
In the realm of medicine and biotechnology, biocompatible materials are driving transformative changes through 3D printing. The emergence of bioinks, specifically tailored to mimic the properties of human tissues, has unlocked new horizons in regenerative medicine. Bioinks facilitate the precise layering of cells and biomaterials, paving the way for the creation of functional tissues and even organs. This groundbreaking technology holds promise for organ transplantation, as it offers the potential to alleviate the shortage of donor organs. Furthermore, bioinks empower researchers to develop advanced drug testing platforms and personalized healthcare solutions, as they can replicate patient-specific tissues for more accurate experimentation and treatment.
“Additive manufacturing has quickly become an essential part of our design and engineering validation process, and continues to be used for more and more functional prototype testing as the technologies advance,” says Dr. Ellen Lee, Technical Leader of Additive Manufacturing for Research & Advanced Engineering at Ford Motor Company.
In the future, advanced materials will spearhead a profound transformation in 3D printing, pushing the boundaries of what is possible. Innovations in materials science will offer an even broader spectrum of options, from super-strong alloys to biodegradable polymers. These materials will empower 3D printing to fabricate intricate, lightweight, and high-performance components with unparalleled precision. In aerospace, this means lighter yet more resilient aircraft parts, while in medicine, it translates to patient-specific organs and implants. Sustainable, recyclable materials will reduce environmental impact, and the convergence of materials and 3D printing will usher in an era of customized, eco-conscious, and innovative manufacturing across industries.