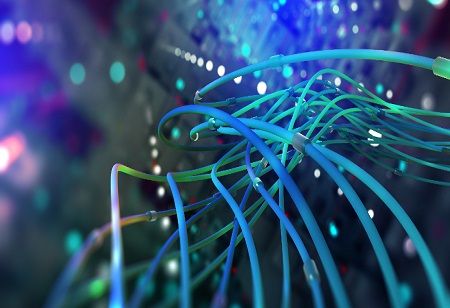
The way we manage data and processes in manufacturing operations has undergone a significant transformation as a result of the digital revolution. Companies are increasingly using the idea of a digital thread to unlock this potent potential as there is advancements in technology. According to Harvard Business Review, modernizing data management and automation procedures will be most beneficial for manufacturers who are just starting their modernization journey. In fact, it's estimated that a lack of digitization results in about $1 trillion in unclaimed assets every year.
Over the past few decades, there have been significant developments in the manufacturing sector. The development of digital thread technology has been one of the most important recent developments. Due to this invention, producers can now track and analyze data more effectively and accurately.
Due to its capacity to increase productivity while lowering expenses related to inventory control and product tracking, it quickly gained popularity in other industries in addition to the automotive sector where it was originally designed as an asset management tool. Digital threads of today are significantly more advanced than those in the past; they allow for real-time monitoring of every stage of production processes while giving businesses insightful data on their operations. Digital thread is revolutionizing the manufacturing industry by offering several benefits that include:
Increased productivity and efficiency
Creating things involves a number of intricate processes. A product rarely develops in a straight line from design and development through manufacturing; change is inevitable and frequently happens quickly. Productivity and quality will inevitably suffer if the design, development, and production teams cannot communicate in real-time.
Digital thread technology can improve productivity and efficiency across the entire production process. Manufacturers can immediately spot bottlenecks and take steps to improve overall performance by connecting the various production phases. Additionally, digital thread technology's automation features eliminate human labour, which boosts productivity and lowers labor costs.
Improved Quality Assurance
The digital thread marks a significant change in the way operations are visualised and how data may be used to inform planned and strategic decisions rather than reactive ones. The digital thread conceptualises all product data from design through prototyping through manufacture and throughout the lifecycle of the product in the field, as opposed to a fragmented and piecemeal approach to systems.
The capability of digital thread technology to maintain quality control throughout the manufacturing process is one of its main advantages. To ensure that materials, components, and products adhere to quality standards throughout their lifecycles, digital threads provide real-time tracking and monitoring. This assists producers in upholding high standards for quality while minimizing waste and material losses as a result of flawed parts or components.
Streamlined Design and Development Cycle
Design engineers can quickly create new goods utilizing current components thanks to digital thread technology, which decreases the time it takes for these products to hit the market. The ability to swiftly make modifications without having to re-manufacture components or start from scratch each time a new version is developed thanks to this technology also makes prototyping simple. As a result, businesses may quickly test out various design concepts without incurring significant prototype expenditures.
Increased Collaboration between teams
Teams from various departments within an organization may effortlessly interact thanks to digital thread technology, which offers real-time access to product data throughout the whole development and manufacturing process.
By ensuring that all parties involved always have access to the most recent information, this prevents the need for duplication of effort, ensures team transparency, and enhances stakeholder communication throughout the product development cycle.
Reduced Risk and Cost Overruns
Manufacturers can identify possible issues early on and address them before they develop into bigger problems later on by connecting all stages of the production process through a digital thread. Additionally, this technology aids producers in more efficient resource management, which lowers cost overruns throughout the life cycle of a project. Additionally, it gives insight into how materials are being used, enabling prompt detection of any irregularities. If ignored, these abnormalities could develop into serious problems that would demand more work or money from the organization.
The technique uses Internet of Things (IoT) sensors to track data from various manufacturing process steps. This data is then sent into analytics software to find issues and areas for development. Additionally, it makes it possible for producers to more effectively manage quality across all manufacturing phases and guarantee legal compliance. More manufacturers are considering integrating this technology into their operations to gain a competitive edge as it continues to progress.
It is evident that the development of digital thread technology has the potential to drastically improve productivity and cut costs across a variety of industries, including the production of consumer electronics, medical devices, and vehicles and aerospace.
We will witness an unparalleled level of precision across each stage of the production cycle as machine learning algorithms continue to evolve alongside improvements in robotics and automation systems as well as smart connected industrial solutions. Thanks to digital thread technology, this will contribute to real benefits for organizations everywhere, including higher profitability due to reduced overhead costs.
All facets of design, engineering, and manufacturing are brought together into one system with the aid of digital thread. As a result, product development times are shortened, goods are of higher quality, customers are more satisfied, and production costs are decreased. Overall, digital thread in manufacturing is lowering waste and errors while increasing industrial processes' efficiency and efficacy.