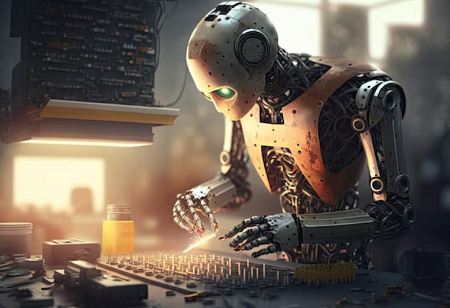
Although humanoid robots are being introduced on a weekly basis, none have demonstrated the same level of speed and precision as the recently launched model by Astribot. The market for AI-powered humanoid robots is becoming as crowded as the cereal aisle in a local supermarket. Just in the past month, OpenAI presented us with two impressive releases. One of the robots, created by Norwegian partners 1X, displayed impressive "soft-touch" skills while folding laundry, while the other robot, developed by partners Figure, showed advanced natural language reasoning abilities. Then in this month, Boston Dynamics impressed us with the incredible agility displayed by its new Atlas robot, and UBTech amazed us with its smooth-talking robot, Walker S. The impressive robots just keep coming.
The incorporation of artificial intelligence (AI) into predictive maintenance plans is transforming the field of robotics manufacturing, bringing about a new age of exceptional efficiency, dependability, and cost savings. In traditional manufacturing environments, maintenance has typically been reactive, involving servicing equipment based on a set schedule or when breakdowns occur, resulting in expensive downtimes and interruptions to production. Nevertheless, predictive maintenance using AI signifies a significant change by utilizing sophisticated analytics and machine learning algorithms to forecast equipment malfunctions preemptively.
Manufacturers can change their maintenance strategy from reactive to proactive by using AI, which allows them to predict problems and address them in advance. AI algorithms examine large amounts of sensor data obtained from robotic systems, identifying trends and abnormalities that could indicate potential malfunctions. This enables maintenance teams to take proactive action by scheduling repairs or replacing components during scheduled downtimes in order to reduce disruptions to production schedules. AI-driven predictive maintenance is completely transforming the field of robotics manufacturing by fundamentally altering how maintenance for equipment is carried out. This is how it is revolutionizing the sector:
Preventing Downtime: Conventional maintenance methods typically include planned maintenance or reacting to breakdowns, which can result in unexpected downtime and decreased production. AI-driven predictive maintenance involves the use of machine learning algorithms to examine data collected from sensors integrated into robotic systems. AI can forecast equipment failure by identifying patterns and irregularities in the data. This allows for maintenance actions to be planned ahead of time and carried out during scheduled downtime, avoiding any unforeseen disruptions to production. Improving Maintenance Schedules: With the use of AI algorithms, historical data can be examined to recognize trends of equipment deterioration and breakdowns. This data enables manufacturers to adjust maintenance schedules according to the real condition of equipment, rather than predetermined intervals. Allocating resources more efficiently and minimizing the impact on production schedules are achieved by performing maintenance only when needed, leading to reduced costs.
Cutting down on maintenance expenses: Proactive maintenance aids manufacturers in preventing expensive sudden repairs by addressing problems before they become significant failures. Manufacturers can minimize the necessity for costly overtime labor and urgent replacement part deliveries by carrying out repairs or replacing components during scheduled maintenance periods. Furthermore, implementing predictive maintenance can help increase the longevity of equipment by detecting problems early on, leading to savings in the long run.
Enhancing Equipment Efficiency: Utilizing AI for predictive maintenance not only detects potential malfunctions, but also offers understanding into the underlying reasons for problems. By examining patterns in data, manufacturers can discover ways to enhance the performance of equipment and anticipate potential breakdowns. This could include making changes to how a system operates, refining maintenance methods, or installing improvements to improve effectiveness and dependability.
“Like the oft-repeated message that AI should augment and assist humans, the same will be true for robotics,” says Stewart Miller, CEO of National Robotarium.
“If you’re using a robot not to replace someone, but to do a job that’s not being done, it’s a completely different equation,” he adds.
Fostering Condition-Based Monitoring: Through AI algorithms, equipment condition can be monitored continuously and in real-time, enabling manufacturers to identify potential failures in advance. AI can detect abnormalities by analyzing factors like temperature, vibration, and energy usage, allowing maintenance teams to receive alerts and proactively address potential issues. Monitoring based on the condition of the system allows problems to be detected early, thus decreasing the risk of major breakdowns and reducing the amount of time equipment is out of service.
“The tremendous advances in artificial intelligence have completely transformed things for us. The remarkable thing is that these advances are directly applicable to robotics, which was a surprise even to me!,” says Geordie Rose, CEO of Sanctuary AI.
Enabling Predictive Analytics: AI-driven predictive maintenance produces large volumes of data that can be utilized for predictive analytics. Manufacturers are able to detect trends and patterns that could impact equipment performance by examining historical maintenance data in conjunction with operational data. This allows them to predict future maintenance requirements, improve inventory control, and use data analysis to enhance overall operational effectiveness.
In conclusion, AI-powered predictive maintenance is revolutionizing robotics manufacturing by moving away from reactive and time-based maintenance methods to proactive, data-driven strategies. Manufacturers can improve efficiency and competitiveness in the industry by using AI algorithms to predict equipment failures, optimize maintenance schedules, reduce downtime, costs, and enhance equipment performance.