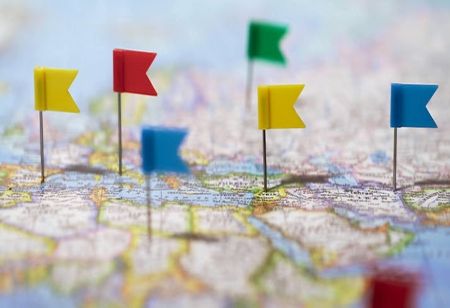
Retail inflation based on the CPI (Consumer Price Index) fell to 4.75% in May from 4.83% in April, as per data from the statistics ministry. While this rate of inflation may fall in the guidelines issued by the Reserve Bank of India, even a tiny fluctuation can create waves in the balance sheets of the players in the manufacturing sector. Inflationary volatility can result in setbacks ranging from increased cost of raw materials to reduced profit margins and sometimes losses. The traditional method of combating inflation by raising prices or implementing cost-cutting measures has already proven to be detrimental in the long run.
Modern day manufacturers have integrated innovative technologies in their operations which have allowed them to combat inflation. They are increasingly taking a nuanced, rather than black-and-white approach to the problematic variables resulting in the aftermath of inflation, here are some tried and tested methodologies deployed by major players to thrive in uncertain economic conditions.
Leverage Advanced Data Analytics
“Data is the oil of the 21st century” is a standard quote emphasized by data experts. Even small-scale manufacturers are beginning to understand the importance of leveraging data in the era of Industry 4.0. Advanced data analytics can provide manufacturers with deeper insights into their operations, supply chains and markets. By virtue of predictive analytics, they are forecasting demand more accurately, reducing their excess inventory and minimizing stock-outs, thus ensuring efficient capital use.
They are also implementing data analytics to identify bottlenecks in production lines, enabling continuous process improvements. This factor has helped them to be resourceful and reduce production costs.
"The ability to capture any data, any time, and anywhere has transformed the ability of manufacturers to uncover real-time issues, recognize patterns that allow them to enhance processes, boost supply chain efficiency and determine variables that impact production, and hence improve operational excellence and cost competitiveness," Dr Richard Lobo, Head - Innovation & CQH, Tata Chemicals.
GE uses advanced data analytics to optimize its operations. The company’s Predix platform collects and analyzes data from its industrial machines, providing insights that help improve efficiency and reduce downtime. For example, GE’s Power division uses predictive analytics to forecast maintenance needs, thereby avoiding costly equipment failures and optimizing inventory management for parts.
Adopt Agile Manufacturing
Major organizations struggle with implementing changes across the spectrum. To combat this, they have developed an agile operative process. The manufacturing sector too is increasingly becoming agile in their responsiveness to the changing market demands and economic conditions. Key components being having a modular production system and a cross-trained workforce.
Implementing a modular production line that can be reconfigured for a variety of products is a tried and tested approach that has allowed manufacturers to have a quick response time to market changes without extensive downtime. This and a workforce that is trained in multiple skills have allowed them to relocate labor as needed, ensuring that operations can continue smoothly when specific roles are impacted by external factors instead of letting go of a trained workforce. “It doesn’t matter how good you are today; if you’re not better next month, you’re no longer agile," Mike Cohn, Co-Founder of Scrum Alliance.
Toyota is a pioneer in agile manufacturing, employing its renowned Toyota Production System (TPS). The TPS emphasizes flexibility, just-in-time production, and continuous improvement (Kaizen). During the COVID-19 pandemic, Toyota's agility allowed it to quickly adapt production lines to manufacture medical equipment such as face shields, showcasing its ability to respond rapidly to changing market needs.
Invest in Automation and Robotics
Automation and robotics has proven to be an excellent one-time investment for almost all the companies that have implemented it. It has reduced a significant amount in their biggest overheads, which is the labor cost. Contrary to popular opinion, automation solutions aren’t about replacing human labor but enhancing their capabilities.
Collaborative robots (Cobots) work alongside their human counterpart, increasing their productivity without replacing them. They can perform repetitive tasks, mitigate the possibility of injuries and free up the human worker’s time so they can focus on more pressing tasks. The robots, coupled with automated quality control, can ensure consistent quality of labor while reducing the costs associated with it. Companies of late, in the aftermath of the AI boom, are leveraging AI to detect defects more; this has proven to be more accurate than human inspectors in a lot of scenarios.
"Knowing what to invest in and ensuring that new methodologies are launched accurately and quickly comes down to three things – what you have, what you know, and who you know," Zoya Brar, Founder, CORE Diagnostics.
Siemens has heavily invested in automation and robotics at its Amberg Electronics Plant in Germany. The plant is a showcase of Industry 4.0, where 75% of production processes are automated. Siemens uses collaborative robots (cobots) to work alongside human workers, enhancing productivity and ensuring high quality through automated quality control systems.
Strengthen Supply Chain Resilience
The Suez Canal crisis of 2021 highlighted the fragility of the global supply chain, bringing virtually every industry to a halt. Supply chain disruptions can be devastating, especially during inflation and other economic crises. Building a resilient supply chain has climbed the ladder in terms of priority for manufacturers due to this incident. Relying on a single supplier increases vulnerability. By diversifying the supplier base, manufacturers can dilute their risk and negotiate better terms. This also has an added benefit to the local suppliers as it can reduce their lead times and transportation costs.
Apple has developed a highly resilient supply chain by diversifying its supplier base and maintaining close relationships with its suppliers. The company uses blockchain technology to enhance supply chain transparency, ensuring that materials are sourced responsibly. During the chip shortage crisis, Apple’s strategic stockpiling of critical components helped it navigate supply disruptions better than many competitors.
"Standardization is the key to creating efficiencies in Logistics,” Vivek Arya, Managing Director, Rhenus Logistics India.
Historically, there has been a recession nearly every decade, and it has been overcome. But, it has resulted in a lot of casualties. And the ones that survived it were the ones who changed the ways they operated to adapt to the new challenges that they were faced with. There has always been uncertain variables around every corner, it is a costly affair to not be prepared to tackle the oncoming variables.