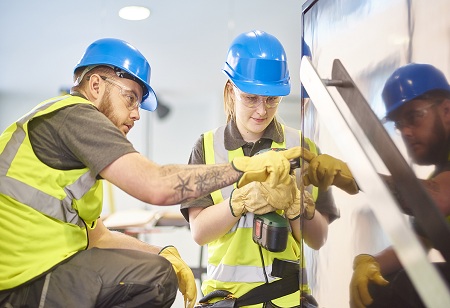
Manufacturing companies must identify and address potential hazards in their workplace. They should use a comprehensive approach which includes conducting a risk assessment, implementing safety protocols, training employees, and investing in safety equipment and technology. Regular inspections should also be conducted to ensure that all safety procedures are being followed. This is because workplace safety is essential for keeping employees safe and healthy. It also helps ensure that businesses are compliant with all relevant safety regulations, which are necessary for protecting workers and preventing costly fines or legal action.
Employers should ensure that their workplace safety protocols are updated regularly to keep up with any changes in regulations. It is also important to provide adequate safety training for employees to ensure their safety and to help protect the business from potential legal action. Employers should consider investing in safety equipment, such as personal protective equipment, to reduce injury risk and safeguard employee safety. Furthermore, employers should regularly inspect the workplace for hazards and take the necessary steps to minimize or eliminate them. For instance, employers should provide employees with safety glasses, hard hats, and steel-toed boots when working in areas where there is a risk of falling objects or hazardous chemicals.
The manufacturing industry is essential to the economy, providing jobs and producing goods that people rely on. However, this industry can also be a hazardous environment for workers. Hazards can range from exposure to chemicals and physical hazards to noise pollution and ergonomic issues. To maintain a safe workplace, it is crucial to identify and mitigate potential hazards
Identifying Hazards
The first step in mitigating hazards is identifying them. One of the best ways to do this is to conduct a hazard assessment. A hazard assessment involves a systematic review of the workplace to identify potential hazards. This can be done by analyzing the equipment, work processes, and work environment. One way to identify hazards is to walk through the workplace and observe the work environment. Observe the equipment, how it is used, and how it interacts with workers. Pay attention to the condition of the equipment and any modifications or repairs that have been made. Observe the work processes and identify any potential hazards. Look for areas of the workplace where employees may be at risk of falls, exposure to hazardous substances, or other physical hazards. Another way to identify hazards is to review the injury and illness records of the workplace. This can provide valuable information about the types of hazards that have caused injuries or illnesses in the past.
Mitigating Hazards
Once potential hazards have been identified, it is essential to mitigate them. There are several ways to mitigate hazards in the manufacturing industry. One way is to implement engineering controls. Engineering controls involve modifying or redesigning equipment or processes to reduce or eliminate hazards. For example, adding guards to machinery or enclosing processes can prevent employees from coming into contact with moving parts or hazardous substances. Administrative controls are another way to mitigate hazards. Administrative controls involve changing the way work is performed or managed to reduce exposure to hazards. This can include job rotation, limiting exposure time, and providing training to employees on how to work safely. Personal protective equipment (PPE) is another way to mitigate hazards. PPE includes items such as gloves, safety glasses, and respirators that protect workers from exposure to hazards. PPE should be used as a last resort after engineering and administrative controls have been implemented. Ergonomic hazards are a common concern in the manufacturing industry. Ergonomic hazards are hazards that can cause musculoskeletal disorders (MSDs) such as back injuries or carpal tunnel syndrome. To mitigate ergonomic hazards, employers should consider redesigning workstations to reduce the risk of MSDs. This can include adjusting the height of workstations or providing ergonomic chairs. Noise pollution is another hazard that can be mitigated. Exposure to loud noise can cause hearing loss and other health issues. To mitigate noise pollution, employers should consider using noise-reducing materials or providing employees with hearing protection.
Training
Training is an essential part of mitigating hazards. Employees should be trained on how to identify and report hazards in the workplace. They should also be trained on how to use PPE correctly and how to work safely around hazardous equipment or substances. Training should be provided to employees on a regular basis, and employers should document that training has been provided.
Identifying and mitigating hazards in the manufacturing industry is essential to maintaining a safe workplace. Employers should conduct hazard assessments to identify potential hazards and implement engineering and administrative controls to mitigate them. PPE should be used as a last resort after other controls have been implemented. Employers should also consider ergonomic hazards and noise pollution when mitigating hazards. Training is a crucial part of mitigating hazards, and employees should be trained on how to identify and report hazards and how to work safely around them. By following these guidelines, employers can maintain a safe workplace for their employees.