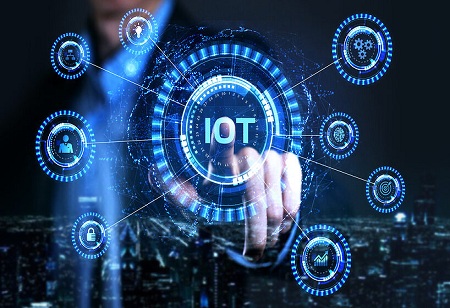
Automation has the ability to increase efficiency and lower labour costs in the industrial industry. It may also eliminate human error and let producers create more complicated goods. Automation in the industrial industry will, in the end, have a substantial influence on the future of employment. Automation can assist to speed up production processes, lowering production costs.
Automation can also assist to minimize the amount of time required to complete particular operations, freeing up workers' time to focus on more difficult, higher-value jobs. Furthermore, automation may lower the amount of energy consumed in production while also improving product quality. Finally, automation may make the workplace safer by lowering the chance of accidents or diseases caused by human mistakes. Although automation has many advantages, it also has certain disadvantages. One of the major disadvantages of automation is the potential for job loss. As computers and robots do duties that were previously performed by humans, there is a risk that certain workers may become obsolete. Furthermore, automation can lead to rising inequality since workers who can adapt to new technologies will see their earnings rise while others who cannot adapt will see their incomes fall American psychologist B.F. Skinner once wrote: “The real question is not whether machines think but whether men do. The mystery which surrounds a thinking machine already surrounds a thinking man.”
The integration of the Industrial Internet of Things (IoT) in the industrial sector has transformed the way industries function in recent years. The Industrial IoT has opened the path for increased efficiency, production, and cost savings by harnessing connected devices, enhanced analytics, and automation. The change in the workforce and the rise of automation in manufacturing processes are two key repercussions of this technological breakthrough.
Enhanced Operational Efficiency
Industrial IoT enables manufacturers to gather real-time data from connected devices and equipment, facilitating better decision-making and operational efficiency. Sensors embedded in machinery can capture information on performance, maintenance needs, and production status, providing valuable insights for process optimization. By leveraging this data, manufacturers can identify bottlenecks, reduce downtime, and enhance overall equipment effectiveness (OEE). Such improvements not only lead to cost savings but also create a more streamlined and efficient manufacturing environment.
Moreover, Industrial IoT enables predictive maintenance, which revolutionizes the traditional maintenance approach. By utilizing sensor data, manufacturers can predict equipment failures and perform proactive maintenance, preventing unexpected breakdowns and reducing unplanned downtime. This predictive approach helps optimize maintenance schedules, extend equipment lifespan, and increase productivity. With fewer manual interventions required for maintenance, employees can focus on more value-added tasks, such as complex troubleshooting or quality control, thereby boosting overall productivity.
Seamless Connectivity and Collaboration
Another crucial aspect of Industrial IoT is the seamless connectivity it offers across different systems, departments, and even supply chains. Through interconnected devices and cloud-based platforms, real-time communication and collaboration among various stakeholders become possible. This connectivity improves coordination between different production stages, suppliers, and customers, leading to more efficient supply chain management.
For instance, connected devices can provide real-time inventory data, enabling just-in-time manufacturing and reducing inventory carrying costs. Manufacturers can receive instant updates on material availability, quality, and delivery schedules, allowing for better planning and scheduling of production. Furthermore, collaboration with suppliers becomes seamless, as IoT-powered systems facilitate automatic ordering, tracking, and supplier integration. The resulting transparency and coordination within the supply chain contribute to faster response times, reduced lead times, and improved customer satisfaction.
In addition, Industrial IoT fosters the integration of humans and machines in a collaborative work environment. With the advent of advanced robotics and cobots (collaborative robots), workers can work alongside machines, complementing each other's strengths. Robots can perform repetitive and physically demanding tasks, while humans can handle more complex and cognitive aspects of the manufacturing process. This collaboration enhances productivity, reduces the risk of human error, and promotes a safer work environment. Moreover, employees can focus on upskilling and reskilling to adapt to the evolving manufacturing landscape, ensuring their continued employability in the era of automation.
Data-Driven Decision Making and Continuous Improvement
Industrial IoT generates vast amounts of data that can be utilized to drive data-driven decision-making processes and continuous improvement initiatives. By leveraging advanced analytics and machine learning algorithms, manufacturers can extract valuable insights from this data, enabling proactive decision-making and optimization of manufacturing operations.
Real-time data analytics can provide manufacturers with valuable information on product quality, yield rates, and overall equipment performance. By analyzing these insights, manufacturers can identify patterns, detect anomalies, and make data-driven adjustments to enhance product quality and yield. This proactive approach minimizes the occurrence of defects, reduces waste, and ultimately leads to higher customer satisfaction.
Industrial IoT enables the implementation of continuous improvement methodologies such as Lean and Six Sigma by providing real-time visibility into process performance. Overall, IoT in industrial automation has the potential to provide enormous advantages to businesses and society as a whole. As a result, it is critical to continue investing in research and development in order to fully exploit IoT's potential in industrial automation. Companies that embrace this technology may enhance their operations, increase production and efficiency, and ultimately build a more hopeful future.