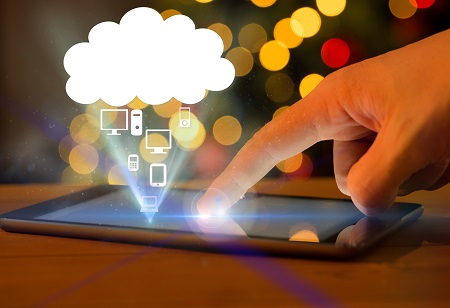
The current Nanotechnology Market Size, equated at USD 5.5bn in 2022, will foresee a market size of USD 84.3bn in 2032, corresponding to a CAGR of 31.8% from 2023 to 2032. Making inroads to nanotechnology in manufacturing procedures indicates a key moment where products can become more precise and process efficiency is raised across various sectors. Primordially, nanotechnology was a process that involved doing very small operations with materials either at the level of molecules or even smaller, such as atoms. The resulting structures had many advanced features that scientists could use to develop products. This brings about new ways of creating excellent products and effectiveness in control systems and resource conservation.
An important consumer benefit the market can provide is improved precision through nanotechnology. It gives manufacturers strong capabilities for making materials with almost unrivaled accuracy and accuracy. After this, designed products are unmatched in longevity, durability, and multi-functionality. Moreover, with this degree of accuracy, very small components or devices can be reduced or even miniaturized, which is of great significance for devices such as EE and M.
Nanotechnology supports producing responsive materials that respond to the surrounding factors, driving the development of a new type of manufacturing, namely, flexible production. This parameter creates productivity of machines in all conditions, and they do not lose their performance over long periods.
Considering that sustainability is a part of this, integrating nanotechnology dictates creating more contributory and eco-friendly processes. Attainable goals involve minimizing material waste, energy usage, and environmental impact and bringing them into concordance with broader efforts to sustain manufacturing the globe over.
These industries can expect higher standards of products that are superior in quality, enhanced production capacity, and a game-changing impact on sustainability methods that give them a competitive advantage in the progress toward technological advancement ahead for others.
Miniaturization for Microscopic Precision
The main perk of incorporating nanotechnology into production lies within its unique capacity to shrink objects to extraordinary micro sizes. This miniaturization process empowers producers to fabricate parts and devices with minute precision, introducing untapped opportunities across numerous industries.
The Da Vinci robot is a multi-armed system with robotic arms fitted with minute surgical tools. These devices are maneuvered from a surgeon's console, making cutting very gentle and detailed inside the patient's body. These robotic components (like the ones in robotic archery) reduce trauma to the patient, speed up recovery times, and improve precision, which cannot be imagined in other surgeries when the surgeon operates through small incisions
This is a representative case of using microtechnology for micromotion and precision in surgery, learning from the experience of technological developments in this field, giving patients non-invasive therapies with more precision and better outcomes.
Advanced Materials with Tailored Properties
The multifaceted characteristics of nanotechnology make customized production more and more possible, which greatly boosts producers' competitiveness, as nanotechnology allows them to develop products with functionality and lastingness that are beyond the wildest dreams of any scientist and engineer. Furthermore, nanotechnologists can now think of ways the physical matter could be shaped to have these special properties. Under this Multiple Supplier Situation, manufacturers gain a lot of space to meet certain rivalry standards.
For example, the Science of Materials Application (SMA) is utilized in biomedicine, mostly in orthodontics; traditional orthodontics usually have standard metal wires, which target specific teeth to apply the required forces to establish the teeth's positions. However, the wire plays the role of redistributing the forces, which needs to be adjusted frequently by the orthodontist to maintain the prescribed level of force.
As SMAs are used, orthodontic wires that can bend or shape in their particular way are made. Depending on the temperature, these threads are set up to revert to their original forms at specific times. Consequently, the tape can be flexed up more flexed up; in this way, it is easier for a clinician to place it. After the placement in the mouth, the wires are heated again to the natural body temperature, which returns them to the previously stored pre-programmed shape, and this tension helps reposition the teeth. It removes repetitive tasks that the orthodontist has to do, i.e., increasing increases and making a comfortable process for the patient.
Smart Manufacturing and Real-time Monitoring
Smart manufacturing is now the manufacturing phase when two-way nanotechnology is applied to production techniques. Sensors and nanodevices are critical to the real-time monitoring and control of these processes because they create the conditions for manufacturers to refine their methods, become aware of problems, and maintain the original quality.
For example: Siemens, a global industrial manufacturing company, uses smart manufacturing technologies and digital twin for real-time monitoring by image and video which is at the same time via digital twin. A digital twin is a virtual counterpart of the physical system or a process in run-time mode with all the data sources in real-time operation mode. Throughout the manufacturing process, Siemens has a digital twin of their production lines and your equipment.
With the help of sensors and connected devices that are installed on the manufacturing equipment, Siemens would collect real-time data (e.g., functionality of machines, energy efficiency, product quality, etc.). The digital twin receives the gathered data which is harmonized into a single and exact representation of the real-time production process.
Through the use of this digital twin, Siemens can gain real-time access to performance control and operational analysis by monitoring and analyzing its production lines. Having the capability to see where the problems exist, improve the process, and reduce spare time by making data-driven decisions are the qualified reasons why they are a good factor for the industry. Take again the example of the digital twin where the digital twin can give information about what is happening such as a machine wear or malfunction. Hence, this contributes to proactive maintenance thus reducing a breakdown.
This whole integration package of smart manufacturing and live monitoring results not just in bettering the efficiency of operations but also in predictive maintenance, resource optimization, and further quality improvement across Siemens' manufacturing processes.
"Integrating nanotechnology in manufacturing processes marks a transformative leap, enabling unprecedented precision at the molecular level. This convergence promises to revolutionize industries by enhancing product quality, efficiency, and sustainability." Says Dr. Sarah Chen, Nanotechnology Specialist and Senior Research Scientist at the Institute for Advanced Materials and Manufacturing.
They brought nanotechnology into fabrication, which is revolutionizing since nanomaterials decisions that conventional methods lack, broadening possibilities across numerous sectors. The capability of submicron manipulation innovates the field by making available the miniaturization of the design characteristics, the emergence of smart fabrics, and the applications of intelligent manufacturing processes. They are given to show through the application of nanotechnology to the manufacturing process that the new product is likely to be more reliable and of better quality than the original.
More and more insight into nanotechnology will become available as its penetration in manufacturing grows. Consequently, industries will devise more strategies to beat the competition, with many companies adopting the latest nanotechnology breakthroughs to have an edge over their competitors. The implementation of these nanotechnology-enabled traits does not equate to a technological modification. Still, it is a strategic tactic for companies with an eye for staying on top amidst an increasingly dynamic and ruggedly competitive environment.