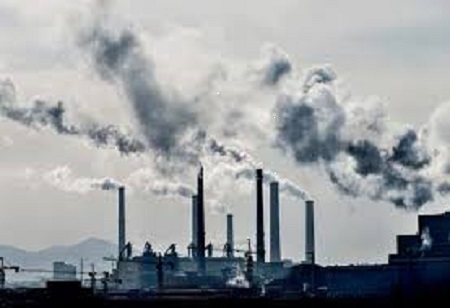
Selective Catalytic Reduction technology is a sophisticated method of lowering hazardous emissions that provides an ecologically beneficial solution to air pollution. SCR technology, for example, is used in diesel-powered vehicles, such as passenger cars and trucks, to minimize NOx emissions, resulting in a cleaner and more efficient engine. However, SCR technology has several limitations. One of the primary drawbacks of SCR is that it can be expensive to incorporate, particularly in older automobiles. Also, during extreme cold scenarios, SCR might not be as effective, resulting in higher NOx emissions. SCR also necessitates the use of a chemical reagent known as AdBlue, which requires to be refilled regularly, raising the overall cost of ownership.
AdBlue is a necessary component for diesel vehicles, but it must be handled with caution. It can be corrosive and lethal for the exhaust system, if not handled properly. Not only must AdBlue be handled carefully, but it must also be stored properly to avoid contamination.
Let us now look at some of the challenges and their possible solutions.
Ammonia Slip
Ammonia is a crucial facet of the Selective Catalytic Reduction system. It reduces nitrogen oxide in the atmosphere to nitrogen and water. However, when the SCR process does not entirely break down the organic material in the wastewater, ammonia slip occurs. This phenomenon poses an environmental hazard due to ammonia's toxicity and its tendency to cause eutrophication in water bodies. Therefore, regular maintenance and monitoring of Selective Catalytic Reduction power plants are essential to ensure that the process is working sufficiently and to identify any potential problems before they become serious. Furthermore, adequate wastewater treatment may be used to ensure that organic material is effectively broken down. This is vital not just to minimize ammonia leakage, but also to keep water bodies healthy and sanitary. If proper maintenance and monitoring is not done, the ammonia slip catalyst can become blocked with soot, which can reduce its efficiency and cause an increase in the amount of ammonia that is released.
Deposit formation
Deposit formation is a common issue for many industrial and commercial facilities. It not only causes technical challenges like clogged pipes, but it can also generate unpleasant odors that can be fatal to health. These scents are triggered by organic debris and bacteria accumulation in pipes and other equipment. It is critical to keep the area around the equipment clean and clear of organic debris to avoid the danger of smells and health problems. In addition, regular cleaning and maintenance of the pipes and other equipment are necessary to prevent deposit formation. This includes using appropriate cleaning chemicals and tools to remove any buildup. It is mandatory to inspect the pipes regularly to ensure that they are in good condition and not allowing deposits to form.
Transportation and storage of Ammonia
Ammonia must be handled and transported with extreme care, due to the safety risks posed by its toxicity and flammability. Storing such a hazardous chemical in large quantities can also be difficult and costly. Additionally, the use of ammonia in SCR systems can lead to an increase in NOx emissions unless properly managed. Furthermore, ammonia can react with the exhaust causing the formation of particulate matter. On the other hand, urea is a less hazardous chemical that can be used in SCR systems. Urea does not form particulate matter when it reacts with exhaust, and it can actually help to reduce NOx emissions.
High cost of investments
Selective Catalytic Reduction requires a large upfront investment in the equipment, installation, and maintenance of the system. For those seeking a cost-effective way to reduce emissions, Selective Catalytic Reduction (SCR) can be the answer. Though the upfront costs of purchasing and installing the necessary equipment and catalysts can be substantial, long-term savings are often achieved with this technology. In addition, the cost of the necessary chemicals and catalysts needed to initiate the reaction can be quite high. For instance, the cost of the Urea solution used in SCR systems can range from $0.50 to $1.00 per gallon, depending on the quantity purchased. Despite the initial costs, SCR is a cost-effective solution in the long run, as it produces fewer emissions and operates at a lower cost than other technologies. It also ensures a reliable and high quality power supply. Additionally, SCR is more efficient than traditional power systems.
Corrosion of Catalysts
Catalysts, like car engines, need regular tender loving care (TLC) to help them perform optimally and avoid erosion caused by flue gases. High-quality materials and protective coatings can go a long way in preserving the efficiency of the catalysts, while regular maintenance and cleaning are essential for keeping them in top condition. Additionally, tweaking the design of the SCR system can reduce wear and tear on the catalysts. Some preventive strategies include using high-quality catalyst materials and applying protective coatings on them. Regular maintenance and cleaning are also important for maintaining the efficiency of the catalysts.
In conclusion , Careful consideration is needed to ensure the technology is utilized correctly for maximum efficiency. Ultimately, the success of implementing SCR technology will depend on careful planning and execution. Therefore, it is imperative to seek expert advice and guidance when considering SCR technology. This can help to ensure the technology is implemented correctly, saving time and money in the long run. It is also important to stay up to date on the latest technological advancements and regulations in order to remain competitive. Ultimately, SCR technology can provide a viable solution for reducing emissions and improving air quality.