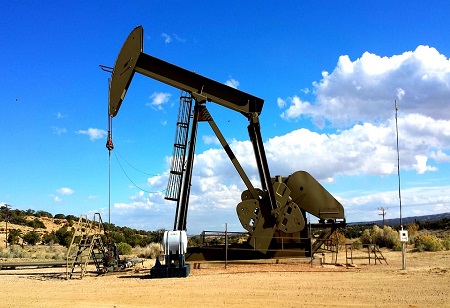
Predictive maintenance is rapidly emerging as a game-changer for the oil and gas industry, revolutionizing how companies manage their critical infrastructure. By harnessing data from sensors and IoT devices, predictive maintenance is enabling proactive equipment monitoring. This data-driven approach is allowing operators to anticipate potential failures and address issues before they result in costly downtime or accidents. The benefits are manifold, from extended equipment lifespan to improved safety and operational efficiency. It is minimizing unplanned shutdowns, optimizing resource allocation, and ultimately boosting profitability. In an industry where reliability is paramount, predictive maintenance is a powerful tool, transforming the way oil and gas companies operate, saving both time and resources.
Over the past three years, the oil and gas industry has seen a remarkable 523,000 patents both filed and granted, as indicated by findings in GlobalData's report titled "Artificial Intelligence in Oil & Gas: Intelligent Predictive Maintenance." A look at its benefits reveals why predictive maintenance is transforming the oil and gas industry for the better.
Minimizing Downtime
Predictive maintenance is swiftly emerging as a crucial way for minimizing downtime in the oil and gas industry. The sector heavily relies on complex machinery and equipment critical for exploration, production, and refining processes. By utilizing advanced data analytics and real-time monitoring, predictive maintenance can identify potential issues, such as equipment wear or malfunction, before they result in costly and unscheduled downtime. This proactive approach allows oil and gas companies to plan maintenance during optimal periods, ensuring the continuous operation of their facilities, preventing catastrophic failures, and optimizing resource allocation. As a result, predictive maintenance is becoming a cornerstone of enhancing efficiency and cost-effectiveness in this vital industry.
An example of how predictive maintenance minimizes downtime in the oil and gas industry is ExxonMobil's use of advanced technologies at their Banyu Urip oil field in Indonesia. The company implemented predictive maintenance strategies, including the use of sensors and data analytics, to monitor the condition of critical equipment, such as pumps and compressors. By continuously analyzing data from these sensors, ExxonMobil's maintenance teams can detect early signs of equipment wear or potential failures. This allows them to schedule maintenance and replacements during planned downtime, optimizing the operational efficiency of the field. As a result, they have significantly reduced unplanned downtime and production interruptions, leading to increased oil production and cost savings.
Enhancing Safety
Predictive maintenance is also playing a pivotal role in enhancing safety within the oil and gas industry. By continuously monitoring equipment and infrastructure, it helps identify potential issues, reducing the risk of catastrophic failures that can lead to accidents, fires, or environmental disasters. Timely maintenance minimizes the chances of unexpected incidents, protecting both personnel and the environment. Moreover, by optimizing the reliability of safety-critical equipment like valves, pressure vessels, and pipelines, predictive maintenance ensures they function as intended during emergencies. Thus, it fosters a proactive safety culture, prevents accidents, and promotes the well-being of workers and the preservation of the environment, making it an invaluable asset in the oil and gas sector.
Petronas Group, Malaysia's state-owned oil and gas company has adopted advanced predictive maintenance technologies to enhance safety at their facilities. For instance, they use predictive analytics and IoT sensors to monitor the condition of critical equipment like pipelines, pumps, and compressors. This allows them to detect potential issues and schedule maintenance before they escalate into safety hazards. By proactively addressing maintenance needs, Petronas reduces the risk of leaks, equipment failures, and operational malfunctions, thus preventing accidents and environmental damage. This approach not only enhances safety but also helps maintain their reputation as a responsible and environmentally conscious energy company in the region.
Optimizing Resource Allocation
As a strategic tool for optimizing resource allocation in the oil and gas industry, predictive maintenance is incredibly useful. By using data analytics and real-time monitoring, companies are accurately assessing the health of their equipment and infrastructure. This enables them to allocate resources more efficiently, directing maintenance efforts and budgets where they are most needed. By focusing on equipment with higher likelihood of failure, they reduce unnecessary spending on over-maintenance and allocate resources for critical components, ensuring they operate at peak efficiency. This approach streamlines operations, lowers operational costs, and maximizes the lifespan of assets, all of which contribute to more effective resource allocation in the oil and gas sector.
Reliance Industries Limited (RIL), one of the largest conglomerates in India with a significant presence in the petrochemical and refining sector, has embraced predictive maintenance. By implementing a range of predictive maintenance technologies, including sensors and analytics, RIL can monitor the health and performance of critical equipment in real-time. This data-driven approach allows them to pinpoint equipment that requires immediate attention, enabling targeted maintenance efforts and allocation of resources where they are most needed. Consequently, RIL has substantially reduced downtime, cut operational costs, and extended the lifespan of their assets. This not only enhances efficiency but also optimizes resource allocation, a vital aspect of staying competitive in the oil and gas industry.
“It is a form of proactive monitoring … on steroids,” said Neisha Kydd, operations safety manager for Shell, Gulf of Mexico.
In the future, predictive maintenance is poised to revolutionize the oil and gas industry even further. As technology continues to advance, the integration of artificial intelligence, machine learning, and the Internet of Things (IoT) will become more sophisticated. This will enable oil and gas companies to achieve a higher level of precision in predicting equipment failures, reducing downtime to almost zero. Furthermore, the integration of drones and remote monitoring will allow for real-time, comprehensive asset inspections in remote or hazardous locations, improving safety and efficiency. Predictive maintenance will also contribute to sustainability efforts by optimizing energy consumption and reducing environmental risks, aligning the industry with global environmental goals.