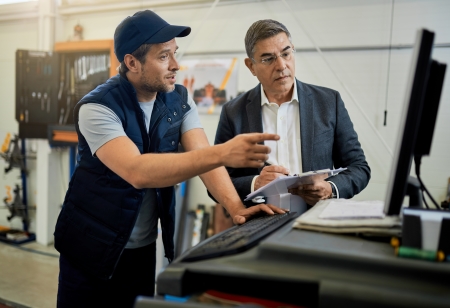
Manufacturing industries are progressively resorting to predictive maintenance as a proactive strategy to ensure consistent success. Through the application of advanced analytics and machine learning algorithms, businesses can proactively anticipate equipment failures and implement preventive actions prior to their occurrence. This saves valuable time and resources and allows manufacturers to maintain optimum production levels and reduce downtime. It enables them to optimize their inventory management by ensuring that spare parts and materials are readily available when needed. Ultimately, this results in improved customer satisfaction as they are able to consistently meet delivery deadlines and provide uninterrupted service.
Reduces Unplanned Downtime:
One of the most significant advantages of adopting Predictive Maintenance is the reduction of unplanned downtime. Traditional reactive maintenance methods often involve waiting for a piece of equipment to fail before addressing the issue. This approach not only disrupts production but can also lead to expensive emergency repairs. Predictive maintenance, on the other hand, leverages the power of data and analytics to predict when a machine is likely to fail. By identifying potential issues in advance, maintenance can be scheduled during planned downtime, minimizing disruptions and ensuring that production continues without a hitch.
Supports Lean Manufacturing:
Predictive maintenance aligns with the principles of lean manufacturing by reducing waste, improving process efficiency, and ensuring resources are used effectively. By way of Identifying potential issues in advance, it helps prevent unexpected machine breakdowns that can lead to wasted time, materials, and manpower. This approach eliminates the need for costly emergency repairs and allows for smoother production flow. Additionally, by optimizing maintenance schedules, helps avoid over or under-utilization of resources, ensuring that they are allocated efficiently throughout the manufacturing process. Overall, Predictive Maintenance contributes to lean manufacturing principles by fostering a production environment that is both streamlined and cost-effective.
Enhanced Operational Efficiency:
Predictive maintenance ensures that equipment operates at maximum efficiency. Such as addressing maintenance needs at the right time, machinery functions optimally, leading to better product quality and increased production rates. For example, in a car manufacturing plant, predictive maintenance can be used to monitor the condition of robotic arms used for welding. By analyzing data on factors such as temperature, vibration, and power consumption, the maintenance team can detect early signs of wear and tear and schedule maintenance before any breakdown occurs. This not only prevents production delays but also ensures that the robotic arms consistently deliver precise welds, resulting in high-quality car bodies and increased overall operational efficiency. Therefore, integrating predictive maintenance into the production environment is essential for achieving a streamlined and cost-effective manufacturing process.
Improved Workplace Safety:
Predictive maintenance contributes to a safer working environment by identifying potential safety hazards or equipment issues before they escalate. This tactical approach not only protects the well-being of employees but also safeguards the company from potential legal and financial liabilities. Furthermore, it helps in implementing preventive maintenance measures that reduce the likelihood of accidents or injuries caused by faulty equipment. Regularly monitoring and analyzing data from the machines, it can detect any anomalies or signs of wear and tear, allowing the necessary repairs or replacements to be made promptly. As a result, employee morale and confidence in their workplace safety are boosted, leading to a more productive and harmonious work environment.
Data-Driven Decision-Making:
Predictive maintenance is more than just a maintenance strategy; it's a treasure trove of data. The insights gained can be leveraged for continuous process improvement. Manufacturers can make data-driven decisions about equipment upgrades, replacements, and process optimizations. This data-centric approach propels companies towards greater competitiveness in the industry. Analyzing the data collected from predictive maintenance, manufacturers can identify patterns and trends that can help them make informed decisions about their equipment and processes. This not only allows them to optimize their operations for better efficiency and productivity but also helps them stay ahead of their competitors.
Facilitates Industry 4.0 Integration:
Predictive maintenance is a key component of the Industry 4.0 framework, where smart manufacturing systems rely on real-time data and automation. Integrating it into Industry 4.0 initiatives can lead to greater overall efficiency and competitiveness. By utilizing predictive maintenance, manufacturers can proactively identify and address potential equipment failures before they occur, minimizing downtime and avoiding costly repairs. This integration also allows for the seamless exchange of data between different systems, enabling a more efficient and streamlined production process. Ultimately, the combination of predictive maintenance and Industry 4.0 technologies enables manufacturers to stay ahead of the competition and meet the demands of an increasingly digital and interconnected world.
Predictive maintenance is a game-changer for modern manufacturing. It minimizes unplanned downtime, aligns seamlessly with lean principles, boosts operational efficiency, enhances workplace safety, and empowers data-driven decision-making. The integration of predictive maintenance with Industry 4.0 positions manufacturers for a competitive edge. Gaurav Taywade, Chief Software Architect, Cemtrex Inc mentions in a blog post published in Nasscom Community- “GPT-based predictive models offer a new frontier in predictive maintenance for the manufacturing industry. By leveraging the power of deep learning and natural language processing, these models enable manufacturers to anticipate equipment failures, minimize downtime, and optimize maintenance activities” In a nutshell, predictive maintenance isn’t just a strategy; it's a path to manufacturing excellence in the business landscape.