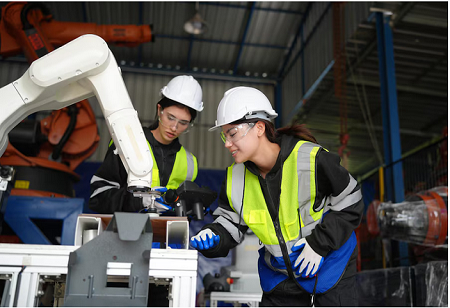
Following a multibillion-dollar takeover by the state-backed Japan Investment Corp., semiconductor materials producer JSR aims to play a leading role in consolidating the industry to keep up with rapid advances in chipmaking. The JIC launched the tender offer on March 19 and completed it Tuesday, offering 4,350 yen ($28.13) per share, according to a Wednesday news release from JSR. Increasing production capacity is a significant challenge for manufacturers globally. However, Asian companies have excelled in this area. By leveraging strategic planning, embracing technological innovations, and maintaining a strong focus on quality, many Asian manufacturers have established new standards for efficient and sustainable production scaling.
"It was a risk for us. We could strengthen our ties with materials suppliers by gaining new know-how for processing and analysis”, mentioned Toru Kimura, Senior Officer at JSR to Nikkei Asia.
Let us now into some of the vital strategic initiatives taken by different Asian manufacturers in order to scale up production and create an example for the global manufacturing ecosystem.
Investments and Strategic Planning
A key takeaway from successful Asian manufacturers is the critical role of strategic planning and significant infrastructure investment. MNCs in the segments of electronics and automotive have exemplified how a long-term vision and staged investments can result in substantial increases in production capacity. They have continually invested in manufacturing facilities and supply chain infrastructure. Their strategies focus on ongoing improvement and the expansion of its production capabilities. By implementing a phased investment approach, they have successfully scaled up production while maintaining efficiency and quality. This strategic planning has been crucial in enabling automotive manufacturers in Asia to produce millions of vehicles each year.
In this segment of strategic investments and planning, Samsung Electronics strategically invests in new facilities and technological advancements. This forward-thinking approach ensures they are well-equipped to meet future market demands.
"Our approach is to anticipate future market demands and align our investments to be ready with the capacity and technology when the market needs it", mentioned Dr. Kinam Kim, CEO of Samsung Electronics' Device Solutions Division.
Technology Planning and Integration
Another important aspect of increasing production is using advanced technology. Many OEMs in Asia have taken smart steps over the years in this regard by using artificial intelligence (AI) and the Internet of Things (IoT) technologies in order to improve production capacity. Adopting smart manufacturing methods has greatly boosted the production efficiencies while keeping all the quality standards high.
By integrating advanced technology, Huawei can optimize its manufacturing processes, minimize downtime, and boost overall productivity. This approach facilitates the rapid scaling of production.
"Technology is the cornerstone of our production strategy. By integrating AI and IoT, we not only scale up our production but also ensure that our products meet the highest quality standards consistently", mentioned Ren Zhengfei, founder and CEO of Huawei.
Continual Focus on Quality Improvement
Keeping quality high while increasing production is a big challenge, but several Asian manufacturing companies have succeeded by using continuous improvement methods. Their automated production systems mechanisms employ lean manufacturing methodologies and aims to remove waste and boost efficiency. This approach, which incorporates methods like Just-In-Time (JIT) and Jidoka (automation with a human touch), ensures that quality remains high even as production levels rise.
"At Toyota, quality is built into every step of the production process. Our commitment to continuous improvement and lean manufacturing has enabled us to scale up production without compromising on quality", mentioned Fujio Cho, Honorary Chairman, Toyota Motor Corporation.
SCM Excellence
Effective supply chain management is becoming particularly essential for increasing production in the Asian markets. Many advanced technologies in terms of GPS connectivity and process automation have disrupted the SCM sector in Asia immensely. In order to create an impeccable SCM system, Asian manufacturers are adapting all the latest methodologies for staying a step ahead in the market.
World's largest electronics contract manufacturer, Foxconn excels in this area to meet the needs of tech giants like Apple. The organization’s skill in coordinating with suppliers and managing logistics efficiently is enabling it to quickly scale up production and expand its presence globally.
"Our success in scaling up production lies in our robust supply chain network. We work closely with our suppliers and use advanced logistics solutions to ensure a seamless flow of materials and components", mentioned Terry Gou, Founder, Foxconn.
Training and Development Initiatives
A skilled and motivated workforce is crucial for increasing production. Tata Steel in India has made significant investments in training and development programs to ensure its employees have the skills needed to meet higher production demands.
As an organization, Tata Steel's emphasis on continuous learning and skill development ensures that its workforce stays proficient in handling advanced machinery and processes, enabling smooth production scaling.
"Our people are our greatest asset. By investing in their training and development, we ensure that they are capable of driving our production scale-up initiatives successfully", mentioned Natarajan Chandrasekaran, Chairman, Tata Sons.
Increasing production is a complex task that involves strategic planning, integrating technology, focusing on quality, managing supply chains efficiently, developing the workforce, and being adaptable. Leading Asian manufacturers like Samsung, Toyota, Huawei, Foxconn, and BYD offer valuable insights on handling these challenges and achieving sustainable growth. By following the examples set by these industry leaders, manufacturers around the world can improve their production capabilities and remain competitive in the global market.