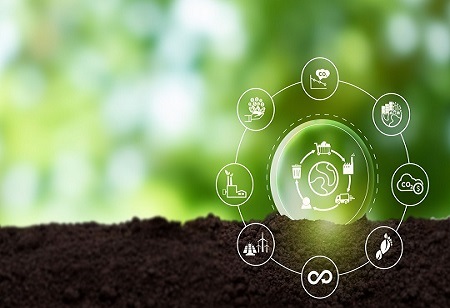
The need for materials and energy has reportedly continued to rise, according to the United Nations Industrial Development Organization (UNIDO). This is due to the industrialized nations' efforts to raise standards of living, support their growing populations, and expand their economies. In response, it is anticipated that by 2050, the manufacturing sector's need for raw materials will be doubled to 180 billion tones.
According to the European Parliamentary Research Service (EPRS), disruptive business models and technologies that boost resource productivity by 30% can help manufacturers transition to a circular economy by the year 2030. Utilizing secondary resources will guarantee the availability of raw materials, reduce reliance on imports, and lessen vulnerability to price volatility.
The 4R's in Circular Manufacturing
The overall waste management hierarchy, which attempts to lessen environmental effect and maximize materials' long-term value retention, is where the 4Rs in circular manufacturing are drawn from.
Rethinking product design to incorporate secondary materials in environmentally friendly production processes and effective waste management is the first step in applying the 4Rs. Each of the 4Rs will have different applications and importance depending on the sector.
Reduce
Lowering the number of materials required for each unit of manufacturing is the first step in reducing material utilization. Innovative design, according to Morseletto (2019), can boost production effectiveness and cut down on material usage. Materials reduction can reduce waste production and resource extraction at the end of the product's lifecycle. According to Morseletto, the global material footprint must be reduced by 80% by 2050. For each sort of substance or energy, targets can be specified.
Materials account for 45% of production costs in Germany, according to a PwC analysis, while energy expenses account for less than 5%. However, if the source relies on fossil fuels, limiting energy use is essential. The reduction of consumption and transition to sustainable manufacturing can be illustrated by a number of examples.
The decrease in packaging-related materials utilized is the most striking example.
Reuse
Reuse is the process of using a good-quality, fully functional product or part to create new ones a second time. Reusing an old product allows it to continue serving its intended purpose while reducing the need to create new ones and extending its useful life. Refurbishing involves upgrading or modernizing a product or component to attain the desired quality and performance.
According to the PwC analysis, recycling and refurbishing might have a significant and complicated impact on the manufacturing industry. In order to reuse or refurbish products on a broad scale, consumer involvement and supply chain modifications, such as reverse logistics and capacity creation to collect used goods, are required. Planning and additional infrastructure will be required for disassembly, storage locations, and part reintegration.
A combustion-powered car's engine can be changed to make it into an electric vehicle as an illustration of refurbishing.
Recycle
Recycling is the process of turning used products or its components into fresh secondary materials. It lessens waste, and the secondary materials are either employed in other industrial sectors in an open-loop system or used in a closed-loop system to create new, unique goods.
At present, recycling is a field that is rapidly expanding. The usage of energy and transportation during the process can have a negative influence on the environment. It can be difficult to recycle composite materials as well. Reusing and refurbishing are more difficult than recycling. And when utilized to close the loop in the manufacturing of the same product, it is quickly emerging as a valuable technique for achieving sustainability in manufacturing industry.
According to reports, the EU wants at least 85% of recycled or reused parts by weight in a vehicle, whereas nations like China, Japan, and Korea seek to recycle 85% to 95% of automotive parts.
Recycling is exemplified by Contec's pyrolysis process, which uses chemcycling to transform used tyres into valuable elements like recovered carbon black, oil, and steel that can be used to create new tyres.
Manufacturers can recover energy from the manufacturing process by incinerating end-of-life products after trying every other option to reduce waste. Recovery has the drawback of destroying the materials, and is only practical with plentiful and affordable waste.
Since some types of plastic are difficult to recycle or reuse, incinerating mixed plastic waste is a common method of energy recovery.
Cost savings, higher sales, establishing a competitive edge, and environmental, social, and governance (ESG) compliance are the most important benefits/top reasons for adopting the circular economy in manufacturing.
Cost Savings
Regardless of which circularity concept a corporation employs, the decrease in resources results right away in cost reductions. According to the PwC analysis, a producer can save up to 60% of the overall material costs by reusing or refurbishing products.
According to EPRS, EU businesses should anticipate material cost savings of between 12 and 23%. That translates into annual savings for the local economy of between €250 and €465 billion.
Secondary raw materials can save 20–90% more energy and a significant amount of water than primary raw materials. Both are significant victories. Secondary raw materials can save 20–90% more energy and a significant amount of water than primary raw materials. Both outcomes are enormous victories for society and the environment.
Creating additional value
The negative effects of manufacturing and hurried consumption are becoming more well known to consumers. Therefore, a competitive advantage goes to any circular product that can demonstrate its sustainability through credible ecological certification and labels. It can aid businesses in capturing and holding onto new market segments.
A third of consumers are reportedly willing to pay more for sustainable components, according to a 2021 Business Wire study. Younger millennials and the Z-generation, whose economic share is growing, are prepared to spend twice as much as previous generations.
ESG Compliance
Globally, ESG compliance is becoming more stringent, and regulations demand that businesses provide comprehensive information.
Because they either assign ESG compliance to a separate department or have different policies for each department, many businesses struggle to meet these obligations. A holistic strategy that incorporates sustainable circular economy principles into the business model can be helpful as opposed to this siloed approach. This will enable businesses to understand how their operations have an influence on the environment.
Corporate governance will be able to be guided by circular business concepts, which will also give the essential specific information because the production process places a high priority on environmental and social problems.
Extracting fresh resources would be less essential if the industry adopted a circular economy strategy. As a result, biodiversity would be protected, pollution would be decreased, marine debris would be collected less, and climate change would be mitigated. According to the EPRS, circular manufacturing can boost the EU's GDP by 0.8% and generate two million new employments.