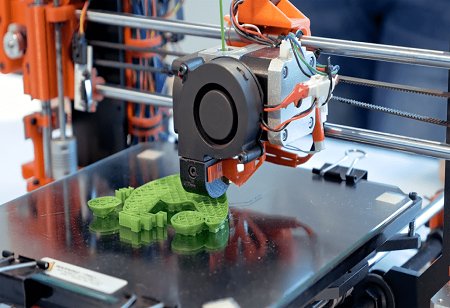
Right from its inception, additive manufacturing has come a long way. Additive Manufacturing provides numerous benefits to both small and large businesses in a variety of industries, thanks to design innovation, mass customization, and on-demand manufacturing. Businesses may bring products to market faster and with fewer investments, allowing them to respond to client needs more quickly.
But how does additive manufacturing affect the environment? Is it less wasteful than traditional manufacturing techniques? Given that most traditional manufacturing techniques are subtractive, resulting in a large amount of scrap material, Additive Manufacturing is an excellent option. Because 3D-printed objects are created without the need of moulds, they require less material, resulting in less waste. Businesses may reduce waste, boost the circular economy, and develop more sustainable manufacturing resources in this manner.
Additive manufacturing in Sustainable production increases the part optimization
Unfortunately, sustainability has become a buzzword that businesses appear to move back and forth throughout their communication platforms. It is a significantly more complex notion that demands thorough comprehension and a high level of devotion. “Since our humble origins, we have been committed to making the world a better and healthier place for future generations” says Fried Vancraen, CEO at Materialise. “Sustainability is about meeting the real needs of the present generation without compromising the ability of future generations to meet their needs,” he adds.
Given that there are few insights into the full impact of additive manufacturing on the environment and people, organizations are dedicated to further exploring the ramifications of this technology. They have broadened their sustainability goals and raised awareness about the relevance of research in recent years.
A lot of companies are looking for innovative methods to develop and implement solutions that will enable them and their customers to be more sustainable by addressing questions like What can be done to make additive manufacturing more sustainable and how can additive manufacturing be applied as the best sustainable choice.
Materialise conducted a life cycle analysis to examine the environmental impact of creating one million pairs of midsoles in order to better understand the impact of our technology and corroborate this assumption. The company evaluated three AM technologies to a traditional production process, conventional PolyUrethane casting, with its partner BASF.
The environmental impact of a commercial product is evaluated at each stage, from raw material extraction to manufacture. The greater the cycle, the less of an impact on the environment. In this regard, 3D-printed objects have the potential to be more advantageous. Because additive manufacturing is built on distinct pieces, it extends the product's life cycle. This enables the incorporation of new components or the enhancement of existing ones, so optimizing and extending the life of the original product. Several variables of longevity are also taken into account, such as the ability to make lighter parts that affect the object's utilization, such as fuel consumption and pollutants.
Reduces waste generation and carbon foot print
Additive manufacturing helps in reducing the waste generation and it also helps in reducing carbon foot print. The LCA investigation concluded that additive manufacturing is more sustainable than traditional manufacturing processes. Additive manufacturing is not clearly a more sustainable option. It has a negative influence on carbon footprint in some circumstances. However, in some cases and for some purposes, additive manufacturing might provide a more sustainable solution. This is significantly dependent on the whole company model, which takes into account materials, transportation, energy usage, resources, procedures, and so on. Using the insoles as an example, we may combine the midsole and the insole into a single customised component, reducing the impact while boosting the value.
Increases team productivity by automating workflow
Today, more than 80% of firms employ additive manufacturing in their operations, primarily for prototyping and in their innovation centres. Companies are hesitant to use additive manufacturing for large-scale manufacturing because they feel it is too expensive, difficult, and time-consuming. One of the major questions is that, "How can businesses be assisted in scaling up their operations in a sustainable manner?"
Materialise Process Tuner is an easy-to-use online tool that assists manufacturers, service bureaus, and machine builders in accelerating the process tuning necessary for mass production 3D-printed products. This helps companies to save money and time by printing hundreds of test samples before determining the best process settings. The Materialise Process Tuner reduces the number of physical test prints necessary to identify the best print parameters. Furthermore, enhanced automation, artificial intelligence, and smart simulations to detect sub-optimal prints enable businesses to scale up their 3D printing operations more sustainably. The Process Tuner is utilised in the production and has saved 50% on the cost of each optimised parameter.
“3D printing has been used in a production context for barely 20 years. So, there are still plenty of innovations to be done. Let’s make them meaningful,” says Fried. "
There is still a lot to learn, and no one can foretell where additive manufacturing will go in the future. Its great potential rests in the many possibilities that are still to be discovered. But one thing is certain: it is up to us to discover new ways that AI may help us construct a more sustainable business while also making a beneficial influence on the planet.