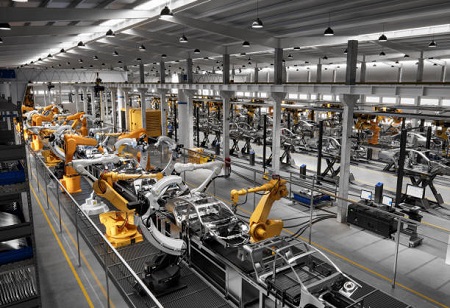
Manufacturing quality is a direct result of the quality control process as a whole. At every stage of the manufacturing process, everyone must be accountable for the pursuit of quality. Not only do high-quality items contribute to the company's integrity, but releasing subpar goods onto the market might have negative legal and financial effects. Before a product leaves the production plant, quality control for manufacturing is in charge of making sure it is free from flaws, that waste is minimized throughout the process, and that it fulfills customer expectations. Systems of compliance as well as testing and evaluation during the manufacturing process are necessary for this.
Enhancing Product Quality and Consistency
Quality standards and compliance measures have a crucial impact on improving the quality and uniformity of products. Manufacturers are required to comply with specific quality standards in order to guarantee their products fulfill predetermined criteria. The scope of these standards can include a wide range of areas within production, encompassing materials, processes, and performance. Manufacturers who adhere to these standards not only meet customer expectations but also foster trust and reliability in their products.
ISO 9001 is a commonly recognized international standard that governs quality management systems. By implementing ISO 9001, companies showcase their dedication to maintaining a consistent delivery of excellent products and services. When the standard is diligently followed, improved product quality and reduced defects can be achieved, as it highlights the importance of processes, customer satisfaction, and continual improvement.
There is a significant advantage in following quality standards as it allows for the early detection and resolution of issues in the manufacturing process. In the realm of automotive manufacturing, the ISO/TS 16949 standard plays a significant role in safeguarding the quality of products at every stage of the supply chain, effectively averting any potential defects and recalls. Not only does this save manufacturers considerable costs related to recalls, but it also protects their reputation.
In addition, product consistency is further enhanced through adherence to quality standards. The purpose of this process is to guarantee that every item produced on the assembly line adheres to the exacting standards. To ensure customers can consistently trust a product's performance and make maintenance and repair easier, consistency is of utmost importance. In industries such as pharmaceuticals, where maintaining consistency is a matter of life and death, adhering to Good Manufacturing Practices (GMP) is not an option but an absolute requirement in order to ensure product quality and safety.
Quality standards and compliance help minimize defects, reduce waste, and enhance operational efficiency. This leads to cost savings and improved profitability for manufacturers." – David Chen, Lean Manufacturing Specialist, UCLA.
Ensuring Safety and Compliance with Regulations
Manufacturers frequently navigate through a intricate network of regulations crafted to safeguard consumers and the environment. These regulations encompass a broad spectrum of elements, ranging from ensuring product safety to evaluating environmental impact. It is imperative to adhere to these regulations without question, as any deviation could result in severe legal consequences, monetary penalties, and harm to one's reputation.
In the food and beverage industry, it is crucial to follow regulations like the Hazard Analysis and Critical Control Points (HACCP) system to guarantee the safety of food. If food safety regulations are not followed, it can result in illnesses, recalls of products, and harm to a company's reputation. The implementation of HACCP enables manufacturers to detect and manage potential hazards in their operations, thereby decreasing the possibility of contaminated products being distributed to consumers.
Strict adherence to Current Good Manufacturing Practices (cGMP) is a legal requirement in the realm of pharmaceuticals. The regulations of CGMP guarantee the safety, effectiveness, and high quality of pharmaceutical products. If one fails to adhere to these regulations, the consequences can be severe, including expensive product recalls, regulatory penalties, and a loss of trust from consumers.
Manufacturing is also greatly impacted by environmental regulations. As environmental concerns grow, businesses face mounting pressure to shrink their ecological impact and curtail waste. Manufacturers can minimize their environmental impact and ensure compliance with local and international regulations by adhering to standards such as ISO 14001, which specifically concentrates on environmental management systems.
Competitive Advantage and Market Access
It is important to note that meeting quality standards and compliance regulations can also give us a competitive edge and open doors for market entry. Customers across various industries have high expectations when it comes to the quality and safety standards of the products they purchase. Manufacturers who are able to consistently deliver products that meet or surpass these expectations gain an advantage in the competition.
For instance, the aerospace sector upholds strict quality and safety requirements, which are crucial for obtaining market entry. In order to satisfy aerospace requirements, companies are expected to comply with standards such as AS9100. Compliance with these standards is frequently a requirement to engage in business with prominent aerospace organizations.
Moreover, in a world connected by global trade, complying with international norms can ease the process of entering and growing in new markets. When companies obtain certifications such as CE marking in Europe or UL certification in the United States, it showcases their dedication to upholding global quality and safety standards. This paves the way for accessing wider markets and attracting a varied range of customers.
Innovation and product development are also influenced by quality standards and compliance. Manufacturers who consistently meet quality standards tend to be in a better position to innovate and enhance their products. Companies can improve and comply with industry regulations to refine processes and create innovative products that meet changing market demands.
The role of quality standards and compliance in manufacturing cannot be overstated. These standards are the bedrock upon which the industry's reputation, safety, and competitiveness are built. By adhering to quality standards, manufacturers enhance product quality and consistency, ensuring that their offerings meet or exceed customer expectations. Compliance with regulations is essential to safeguard consumers, protect the environment, and maintain legal standing. Finally, achieving quality standards and compliance can provide manufacturers with a competitive edge, open new market opportunities, and drive innovation. In today's globalized and fast-paced manufacturing landscape, embracing quality standards and compliance is not just a choice—it's a strategic imperative.