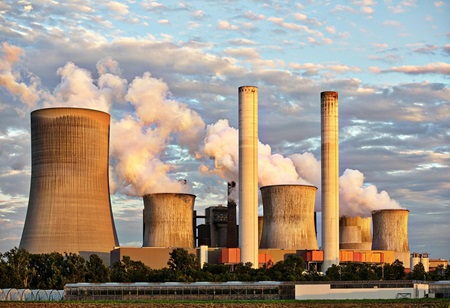
Based on a recent study by Oracle, 55 percent of the manufacturers said that the major manufacturing challenge for them is to enhance the productivity. This statistic serves as an example to the whole industry that the priority is still given to cost effective and efficiency measures. Ensuring a balance between these objectives requires going over obstacles related to the changing demand, supply difficulties, and technical complexities. Investments in automation and workforce training are essential but should be made strategically with some input on the amount of financial resources to be spent. Besides, there are an additional issues of legal compliance and international market dynamics that are added. The challenges can be overcome thorough planning, innovation, and a constant readiness to improve the productivity and optimization of the production ultimately.
Let us analyze three key proven strategies that can be used by manufacturers for maximizing production and cutting costs.
Lean Manufacturing
Lean manufacturing can be a key success factor helping the manufacturers maximize their potential and minimize their costs. Researches demonstrate that companies implementing lean techniques gain a range of benefits, to the extent that a 25-35% reduction of manufacturing lead times and a 20-50% increase of labor productivity are achieved. Lean manufacturing does this by getting rid of waste, by optimizing processes, and by improving the efficiency of manufacturing operations, which leads to a reduction in costs and an increase in the efficiency of the utilization of resources. Furthermore, lean methodologies help to improve the organization, collectively and also engage employees, creating a culture that encourages innovation and problem solving. By means of consistent implementation of lean methods, manufacturers can carry out the simplification of operations, raise the output and make sure the sustainable cost reduction, which in turn leads to the competitiveness in the market of high dynamics.
Lean manufacturing is one of the many cases where production costs are minimized and productivities maximized for production exemplified by Toyota. People are still amazed at the changes that Toyota brought to the industry though the lean production which is a result of the just-in-time production and the continuous improvement. TPS, in turn, enabled Toyota to diminish the lead times, go waste free and improve the quality of the product, which not only led to cost reduction but also productivity enhancement. For that reason, the company has always acquired the status of one of the biggest auto companies on the planet as well as the highest level of productivity and affordable price. The practical example of lean manufacturing in action makes us conclude that lean principles do greatly contribute to the achievement of operational excellence and the long-term success of manufacturing companies.
Investment in Automation
The application of automation in manufacturing provides a way of increase in production at a low cost by eliminating the wastage of product during the processes and the precise routine work. Between automation, the price could lower up to 10-15% and the productivity increased by 20-30%. Robotic technology, artificial intelligence and advanced technologies are used to complete tasks without errors or downtime, thus, reducing the risk of incidents. The automation process also increases the flexibility and scalability in the manufacturing to monitor the changing demand in the shortest period of time. Despite the initial costs that are sometimes considerable, the long run benefits, which come in terms of productivity gains and efficiencies in resource allocation, far outweigh the cost, hence guaranteeing sustained competitiveness and profitability in the manufacturing sector.
A case of how investment in automation had led to productivity enhancement and cost reduction is very much evident in the activities of Foxconn, a large scale electronics manufacturer. Foxconn expanded automation significantly in their factories, especially for assembly lines like the ones of iPhones. Using robots and an automated processes it has been possible for Foxconn to get significant efficiency gains and to reduce the labor costs by up to 30% and increase productivity by more than 100% in some areas. This move not only increased Foxconn’s output but also enhanced its quality and consistency, resulting in the company’s ability to meet the enormous demand for consumer electronics while retaining competitive pricing in the global market.
Supply Chain Optimization
The optimization of the supply chain allows manufacturers to be productive and utilize the least possible resources in order to be effective while dealing with competitive costs by improving responsiveness and efficiency of the whole supply chain. Research shows that through efficient supply chain management it is possible not only to get cost reduction of 10-30% but also to have delivery improvement of 20-50%. Through the application of smart replenishment programs, best supplier practices, and an efficient supply chain, manufacturers are able to shorten the lead times, improve the service level and reduce the amount of inventories. Smart technologies such as blockchain and AI supply the system of real-time monitoring and predicting analytics and help to make proactive decisions and minimize risks. Using supply chain optimization, manufacturers will have the chance to achieve the operational excellence and this will make their profits and competitiveness in the current dynamic business environment.
Notably, the contribution of supply chain optimization is also proved by Walmart, a real-life example. By way of its functional Retail Link system and partnership with suppliers, the Walmart supply chain was able to both minimize costs and maximize efficiency. With these advanced forecasting algorithms and updated stock management practices, Walmart has succeeded in decreasing stockouts by 16% and inventory worth $3 billion. By optimizing its network, Walmart was able to improve on-shelf availability and reduce stock-out, carrying costs, and waste. The company's supply chain management was the fundamental factor to secure its leadership position in the retail industry, which can be considered as the amazing power of supply chain optimization.
“Manufacturers are constantly seeking ways to optimize their operations and enhance productivity as a means of fighting in increasingly competitive environments. One key metric at the heart of this effort is Overall Equipment Effectiveness (OEE) – but too many manufacturers have not made optimal use of OEE.” - Sean Riley, Global Industry Director for Manufacturing & Transportation at Software AG
To understand the manufacturing of the future, we must comprehend the role that advanced technologies such as AI, robotics, and IoT will play as they are continuously integrated to optimize production at the lowest possible cost. The Industry 4.0 will be staged of the most advanced forms of automation and connectivity, providing the next generation factory with the real-time data analytics and predictive maintenance capabilities. With the advent of collaborative robots (cobots), humans will be able to work together, hence enjoying the advantages of agility and productivity. Blockchain and digital twins will contribute to a supply chain that is more flexible and resistant, therefore improving inventory management and cutting the lead time. Along with this, sustainable practices will have top priority, renewable sources of energy, and the circular economy principles will be used, that will drive cost savings and environmental protection.