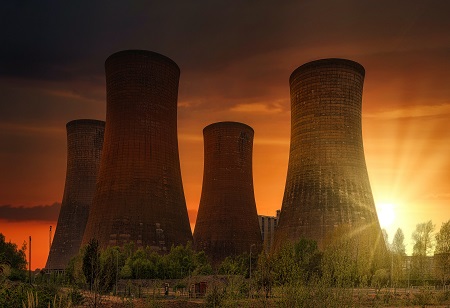
Worldwide, the manufacturing market is set to expand. Predictions say it'll grow by an eye-catching 16% yearly from 2023 to 2032. Companies today are focused on improving their production systems, all while sticking to a budget. This trend is a move to get better at what they do without spending too much money. There's a growing demand for affordable ways to update manufacturing processes, which has brought growth to the market. Businesses seek new ideas to modernize machinery, simplify procedures, and utilize new tech. Manufacturers examine methods like automation, using less energy, and integrating digital systems. The goal is to operate better in a way that also saves money. This active industry scene shows a growing demand for affordable yet effective solutions. This leads to an increase in developing and using low-cost upgrades across many businesses.
The COVID-19 pandemic made the use of digital tech grow in many industries and areas, which caused an even bigger rise in the demand for digital infrastructure.
In manufacturing, staying updated with tech advancements and facility upgrades is vital to keep in the race. But not all firms have a hefty budget for big updates. Even then, with smart planning and a push for efficiency, you can still boost your manufacturing setup, even on a small budget.
“Innovations in artificial intelligence (AI), machine learning, and the industrial internet of things (IoT) all have the potential to save the sector an estimated $373 billion by 2025 by automating machinery operation, facilitating predictive maintenance, improving traceability, harnessing the power of real-time data and analytics, and providing visibility across the mine-to-market value chain. “Says Mr. Dharamdev Rajwar, Regional Sales Manager- Mining, Aluminium and Cement Southeast "
Optimizing Key Elements: A Priority Guide
When money is tight, it's essential to focus improvements on areas that will best boost efficiency and job performance. Pinpointing key areas where betterment is needed helps wisely use resources.
Lean manufacturing aims to trim wastefulness while maximizing processes for better efficiency, even without deep pockets. Spotting weak points in workflows enables makers to make actionable updates with meaningful results.
For example, Toyota in the 1950s showed real-world lean principles in action. They changed the manufacturing game with their Toyota Production System (TPS). It aimed to scrap all forms of waste. Persistent upgrades and a driven efficiency mindset allowed Toyota to polish its manufacturing lines and see remarkable boosts in productivity without splurging.
Embrace Technology within Budget Constraints
Technology is key in current manufacturing. It brings chances for machine control, observing data, and improving processes. Even if fancy technology seems too costly for low-budget firms, they can still use tech without spending too much.
People often think automation is expensive. But, tech progress has made it more reachable to smaller manufacturers. Factories can simplify recurring jobs and boost efficiency by putting money into affordable automation like friendly robots or basic conveyor systems.
Take Acieta, a company that provides robot-powered help, as an example. They supply affordable automation aids made for smaller and medium sized factories. This enables these manufacturers to add automated processes without a huge financial commitment. When they choose automation within their spending limits, manufacturers can see clear enhancements in their work output and ability to compete.
Leverage Partnerships and Collaborations
Working with outside groups and using what's already available can help improve factory systems without breaking the bank. This can mean teaming up with product providers, schools, or government. Manufacturers get to learn more and have extra help in getting better.
Product providers can be great pals in making factory systems better. Manufacturers can get special services and know-how by forming smart partnerships with them. These can give a big boost to how things work.
Boeing's cooperation with its suppliers in the aerospace sector serves as a prime example. They improve lean methods, boost supply chain productivity, and consistently enhance Boeing's production methods. Boeing improved its production framework without significant extra costs thanks to supplier collaboration on fine-tuning processes and introducing novel ideas.
Improving factory systems on a tight budget needs careful planning. It's about picking vital upgrades, using tech within budget limits, and getting help from partnerships. If you focus on being efficient, creative, and resourceful, you can greatly boost productivity. You can be more competitive without spending too much. The journey might be tough, but the payoff is a better, modern factory. It's worth the effort and resource use.
To wrap up, victory needs good thinking and practical actions. It's about making the most of every dollar you spend to build a more flexible, competitive, and tougher factory operation.